Contents
The Role of Safety Data Sheets in Compliance Readiness
8 May 2025 - Evotix
In July 2021, an incident at a chemical manufacturing company based in Decatur, Alabama, resulted in a tragic incident where two workers died and another was hospitalized due to a respiratory hazard exposure. The company, Daikin America Inc., failed to perform air monitoring to assess chemical exposures, provide written procedures that clearly identified the required level of respiratory protection and communicate to workers the hazards associated with the chemicals. As a result, the U.S. Department of Labor's Occupational Safety and Health Administration (OSHA) cited Daikin America for 10 violations and proposed penalties totaling $232,000.
This unfortunate incident highlights the critical importance of proper chemical management and hazard analysis. Maintaining accurate and accessible safety data sheets (SDSs) serves as a frontline resource in protecting workers from chemical-related hazards.
What Is a Safety Data Sheet?
According to OSHA, safety data sheets are documents that “include information such as the properties of each chemical; the physical, health, and environmental health hazards; protective measures; and safety precautions for handling, storing, and transporting the chemical.” In other words, SDSs allow workers to access all essential information about chemical and hazardous substances in a comprehensive way. Without such, organizations expose themselves to potentially fatal outcomes and put their workers in harm's way. SDSs help support safety training and emergency response protocols and are often the first reference point when questions arise about how to safely manage a substance.
Who Requires SDS Management?
Proper SDS management is mandated by OSHA 1910.1200 for organizations operating in the U.S. and Regulation (EC) No 1907/2006 for organizations operating in the EU. These regulations require any organization that stores, handles or uses hazardous substances to maintain an accurate and accessible SDS for each required substance. This includes ensuring SDSs are readily available to all employees, written in a clear and understandable manner and reviewed and updated on a necessary basis.
What Must Be Included in an SDS?
The mandatory sections for SDS management required by both OSHA and REACH are listed in Appendix D to § 1910.1200 and Article 31 of Regulation No 1907/2006:
-
Section 1: Identification
-
Section 2: Hazard Identification
-
Section 3: Composition/Information on Ingredients
-
Section 4: First Aid Measures
-
Section 5: Fire-Fighting Measures
-
Section 6: Accidental Release Measures
-
Section 7: Handling and Storage
-
Section 8: Exposure Controls/ Personal Protection
-
Section 9: Physical and Chemical Properties
-
Section 10: Stability and Reactivity
-
Section 11: Toxicology Information
-
Section 12: Ecology Information
-
Section 13: Disposal Considerations
-
Section 14: Transport Information
-
Section 15: Regulatory Information
-
Section 16: Other Information, Including Date of Preparation or Last Revision
What Is the Purpose of an SDS?
Safety data sheets play a crucial role in ensuring workplace health, safety and compliance through the following ways:
1. Protection
The primary purpose of SDSs is to ensure workers are aware of the risks associated with the chemicals they work with. When workers understand the potential hazards, they can take appropriate precautions, such as using personal protective equipment (PPE) or following specific handling procedures, to prevent accidents and injuries.
2. Storage and Handling
SDSs provide essential guidelines on the proper storage and handling of hazardous substances. This information helps organizations prevent accidents including chemical spills, fires or explosions, which can happen if substances are stored incorrectly or mishandled.
3. Emergency Response
In the event of an emergency, such as a chemical spill or leak, having accurate and accessible SDSs is crucial. These documents outline the necessary steps for containing and mitigating the adverse effects of a hazardous substance. SDS management ensures an organization effectively outlines emergency procedures.
4. Compliance
Regulatory compliance is a key reason for maintaining up-to-date SDSs. Local, national and international regulations mandate that hazardous chemicals be documented, handled and disposed of in specific ways to protect both people and the environment. Failing to comply with these regulations can result in severe penalties, legal action, reputational damage, serious injuries and even fatalities.
5. Risk Management
Accurate SDSs are essential for conducting comprehensive risk assessments. By understanding the risks associated with each chemical, businesses can identify potential hazards and implement measures to mitigate them. It is crucial for everyone to be aware of the chemical risks and hazards to prevent accidents and ensure new or unfamiliar substances are handled safely.
Common SDS Compliance Violations
Despite the clear importance of SDS management, many businesses fall short in their compliance efforts. Common violations include:
1. Incomplete SDSs
Failing to maintain a complete set of SDSs for all hazardous substances can happen when new chemicals are introduced without adding the corresponding SDS to the database.
2. Outdated or Inaccurate SDSs
Chemical formulations and regulations change over time. Using outdated SDSs can lead to improper handling and storage practices, increasing the risk of accidents.
3. Lack of Resources and Documentation
Some businesses fail to allocate sufficient resources for SDS management, leading to disorganization and incomplete documentation. This lack of investment can result in serious compliance issues and increased safety risks.
The consequences of these violations can be severe. Regulatory bodies can impose hefty fines for noncompliance. Additionally, incidents that could have been prevented with proper SDS management, especially incidents leading to injury or death, can result in lawsuits, financial losses and irreparable damage to a company’s reputation.
The Cost of Noncompliance
In 2023, workplace injuries cost businesses over $58 billion in direct costs. However, the indirect costs of workplace accidents can sometimes extend up to 20 times that of the direct costs, putting extreme financial strain on an organization. But beyond the financial impact, the cost of a human life is immeasurable. No dollar amount can truly account for the loss of life, long-term health effects or emotional toll these incidents place on families, coworkers and communities. Prioritizing safety through robust SDS management is not just a legal obligation, it’s a moral one.
Given the complexity and importance of SDS management, relying on manual processes or outdated systems is a risky approach. Managing your SDSs as part of your EHS management processes helps you streamline all your risk management activities. The right software solution can streamline and improve SDS management through greater efficiency, increased visibility, live compliance updates and track and search capabilities.
The cost of noncompliance with SDS regulations is too high to ignore. By investing in future-proofed SDS management practices and leveraging the right software, businesses can ensure compliance, protect their workforce and minimize risks.
Learn more about how an investment in proper SDS management safeguards the safety and success of your organization below!
RELATED BLOGS

The Ultimate Guide to Chemical Management
23 January 2025 - Evotix
From manufacturing to agriculture to healthcare, handling chemicals is a routine part of operations in many industries. However, it comes with its own set of challenges and hazards. For instance,..
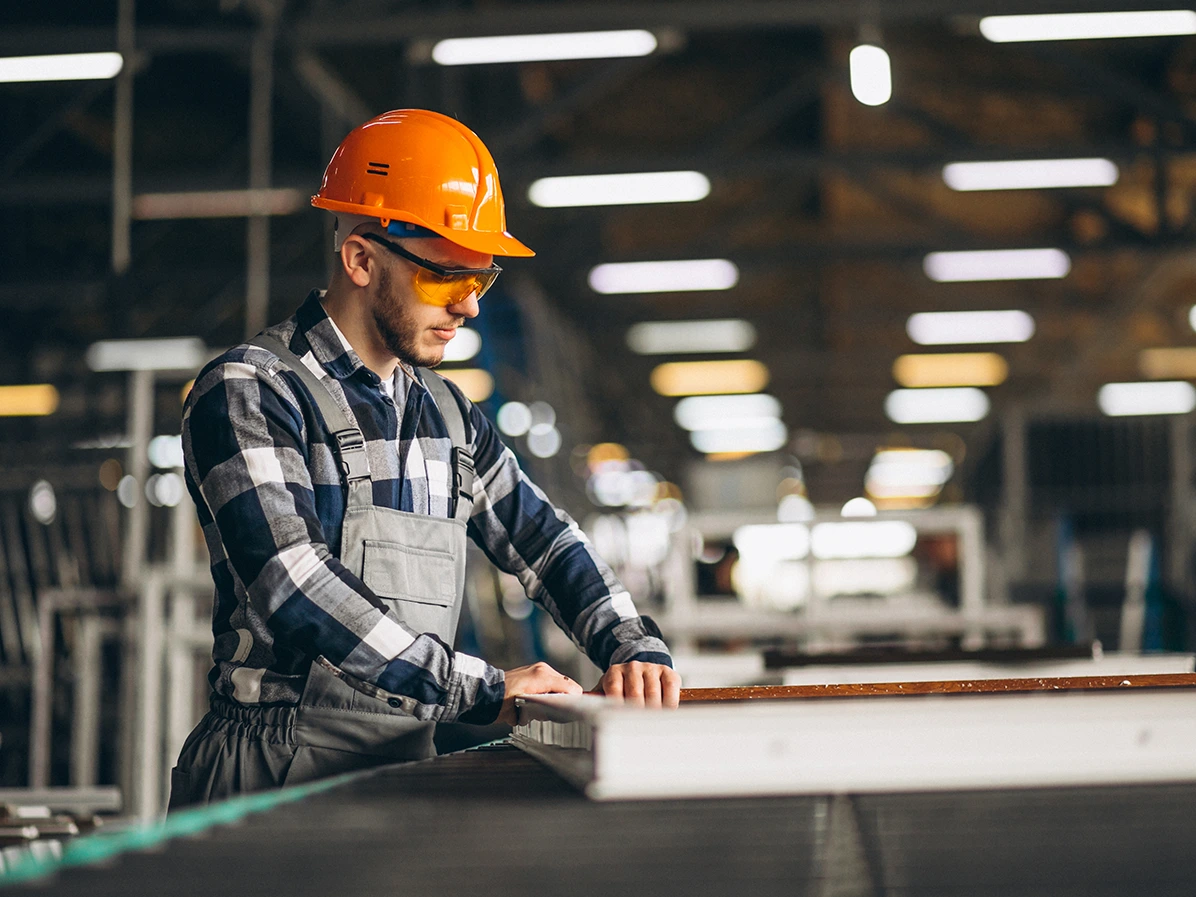
How To Ensure Good Health And Safety Practices In Manufacturing
1 December 2022 - Evotix
The manufacturing industry is an economic powerhouse in the U.S. It’s responsible for producing 20 percent of the nation’s capital investment, 35 percent of productivity growth, 60 percent of..
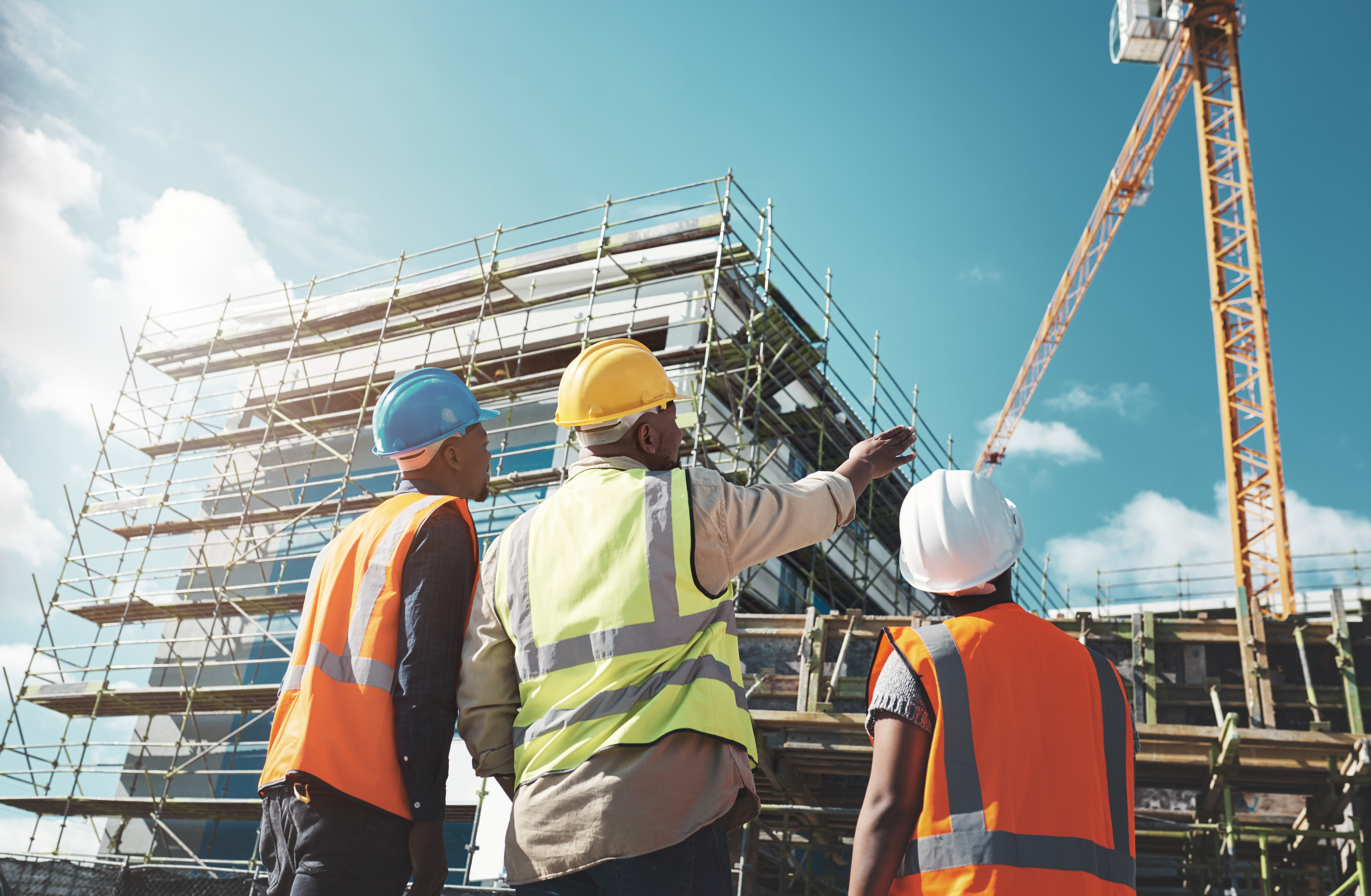
Tips for Elevating Contractor Safety To Meet Growing Demand
9 January 2024 - Evotix
Contractor safety management is a highly important framework for companies navigating an era of increasing dependence on contractors. But what exactly is it? It's a fusion of integrated management..