Contents
What To Include in Your Workplace Emergency Action Plan
24 April 2025 - Evotix
Being prepared for unpredictable emergencies can be a challenge, but it’s vital. Workplaces often bear significant losses as a result of natural disasters, emergencies and unexpected events. An organization’s location, workforce size, building layout and the use of dangerous materials or machinery all contribute to the need for unique emergency procedures tailored to each potential scenario.
These procedures are known as emergency action plans (EAPs).
What Is an Emergency Action Plan?
An emergency action plan (EAP) is a written plan that organizes employer and worker actions during an emergency. An EAP may also be referred to as an emergency response plan or an emergency procedure. Detailed, thorough EAPs are the hallmark of a proactive approach to health and safety management, which helps identify and resolve workplace hazards before they can cause incidents.
Developing an EAP can boost your organization’s ability to withstand the risks presented by disasters and minimize injuries, illnesses, damage and losses. EAPs often include features such as workplace floor plans, procedures for reporting emergencies and dedicated assembly locations.
Who Should Create an EAP?
In the U.S., emergency action plans are a requirement for all organizations that fall under OSHA standards. In the U.K., HSE requires an EAP for all businesses.
While your organization’s leadership and EHS professionals are central to the creation of an EAP, everyone at your workplace should be involved in the process.
Employees are often overlooked in the creation of an EAP. However, just as they are uniquely situated to notice hazards that might be missed by management, employees may be able to judge the effectiveness of preparations more accurately than leadership.
Working directly with the machinery, vehicles and/or materials on your site can give employees insight into the preparations that may be needed in the case of a disaster. For example, an employee may be able to recommend that a particularly dangerous machine be shut down during emergency preparations to minimize damage to the site when a disaster strikes.
How Should EAPs Be Communicated to Employees?
An EAP can only help minimize the damage and losses incurred by an emergency when properly communicated to everyone in your workplace. Employees and management need to understand their roles and responsibilities in case of an emergency.
OSHA recommends that copies of an EAP be distributed to all employees or placed in a central location where employees can find them in case of an emergency. If an organization employs fewer than 10 employees, OSHA allows EAPs to be communicated verbally.
It’s important that your EAP is specific, straightforward and easy to comprehend. When it comes to EHS procedures, simple is always better.
What Should EAPs Include?
Emergency action plans may vary based on regulatory bodies, but should include most of the following information:
-
A preferred method and/or procedures for reporting fires and other emergencies
-
Designated emergency escape procedures and route assignments, such as floor plans, workplace maps and safe or refuge areas
-
Procedures to account for all workers after an evacuation, such as designating an assembly location (e.g., a safe/refuge area)
-
Names, titles, departments and phone numbers of individuals both within and outside the company to contact for additional information or explanation of duties and responsibilities under the emergency plan
-
Procedures for employees who must perform critical operations or essential services, such as equipment shutdown or fire extinguisher use, before evacuating
-
Rescue and medical duties for any workers designated to perform them
How To Develop an Emergency Action Plan
1. Identify the risks of the disasters most likely to occur. These location-specific disasters will help to dictate the procedures your organization needs to create. For example, an organization located in a coastal city will more likely experience a hurricane while a business based in a frigid location will more likely experience a blizzard.
2. Include a diverse group of representatives. OSHA recommends that you include management, workers, local health departments and agencies and public safety officials/members in the planning process. If a specific individual is needed when the plan is carried out, that individual should be present as the plan is being created.
3. Designate response leaders. Communicate with these leaders and make sure they’re aware of their roles and responsibilities.
4. Develop a shelter and/or evacuation strategy. Everyone should know how to evacuate and where to go.
5. Mark the location of emergency supplies. Make it clear where they reside, regularly review supplies and make sure items don’t expire.
6. Establish communication channels. OSHA states that “the employee alarm system shall be distinctive and recognizable as a signal to evacuate the work area or to perform actions designated under the Emergency Action Plan.”
7. Review your EAP regularly and when changes are made. When changes are made in your workplace, such as the installation of a new machine or vehicle, it’s important to review your EAP and make any necessary changes. Remember, include any employees directly involved in the change in the review.
8. Practice often. Ensure that your entire organization is participating in regular, thorough emergency response practices.
Creating, distributing and following an EAP is the most effective way to protect your workers and your workplace from the damages and losses that a disaster could cause.
Emergency Preparedness and Response Software assists organizations in creating and maintaining EAPs. For more information, visit our solution page below.
RELATED BLOGS
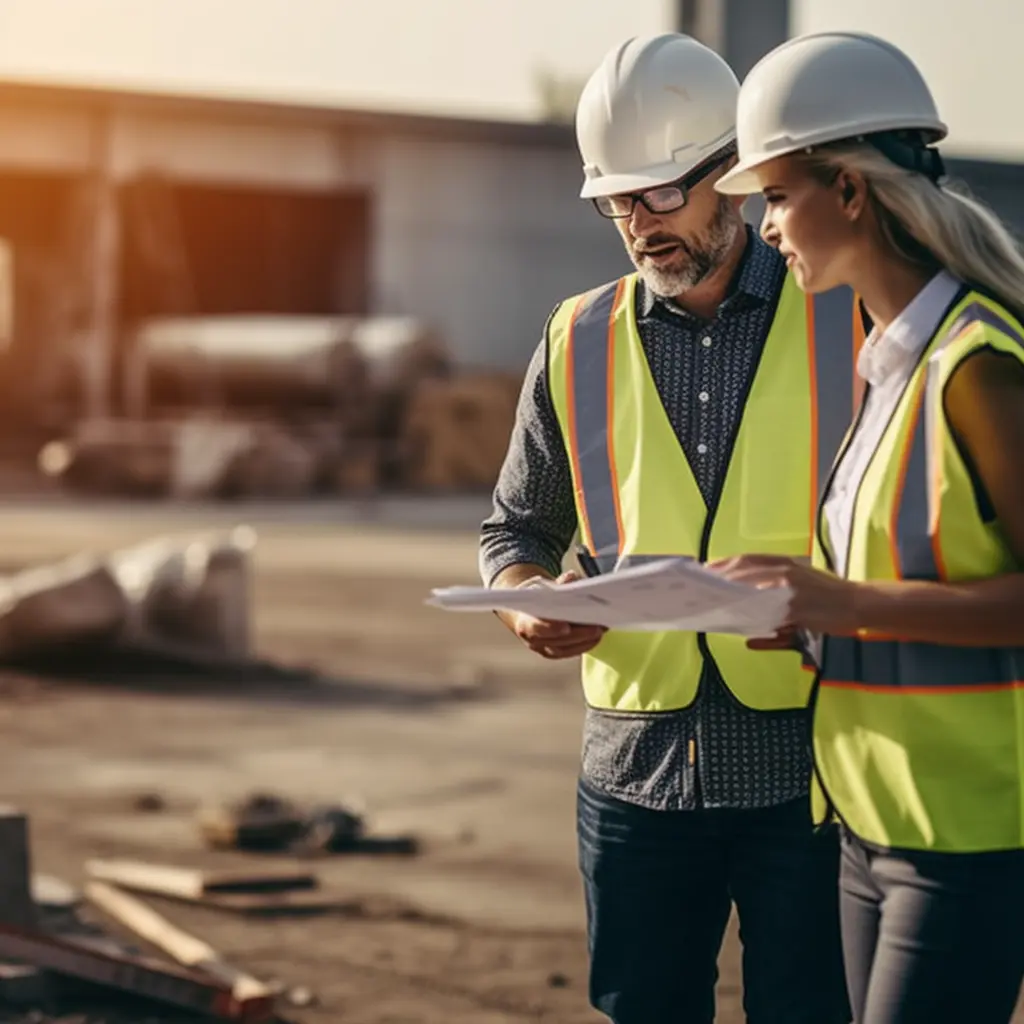
The Ultimate Guide to EHS: What It Means and Why It Matters
7 January 2025 - Evotix
Before diving in, let’s clarify a few key acronyms.
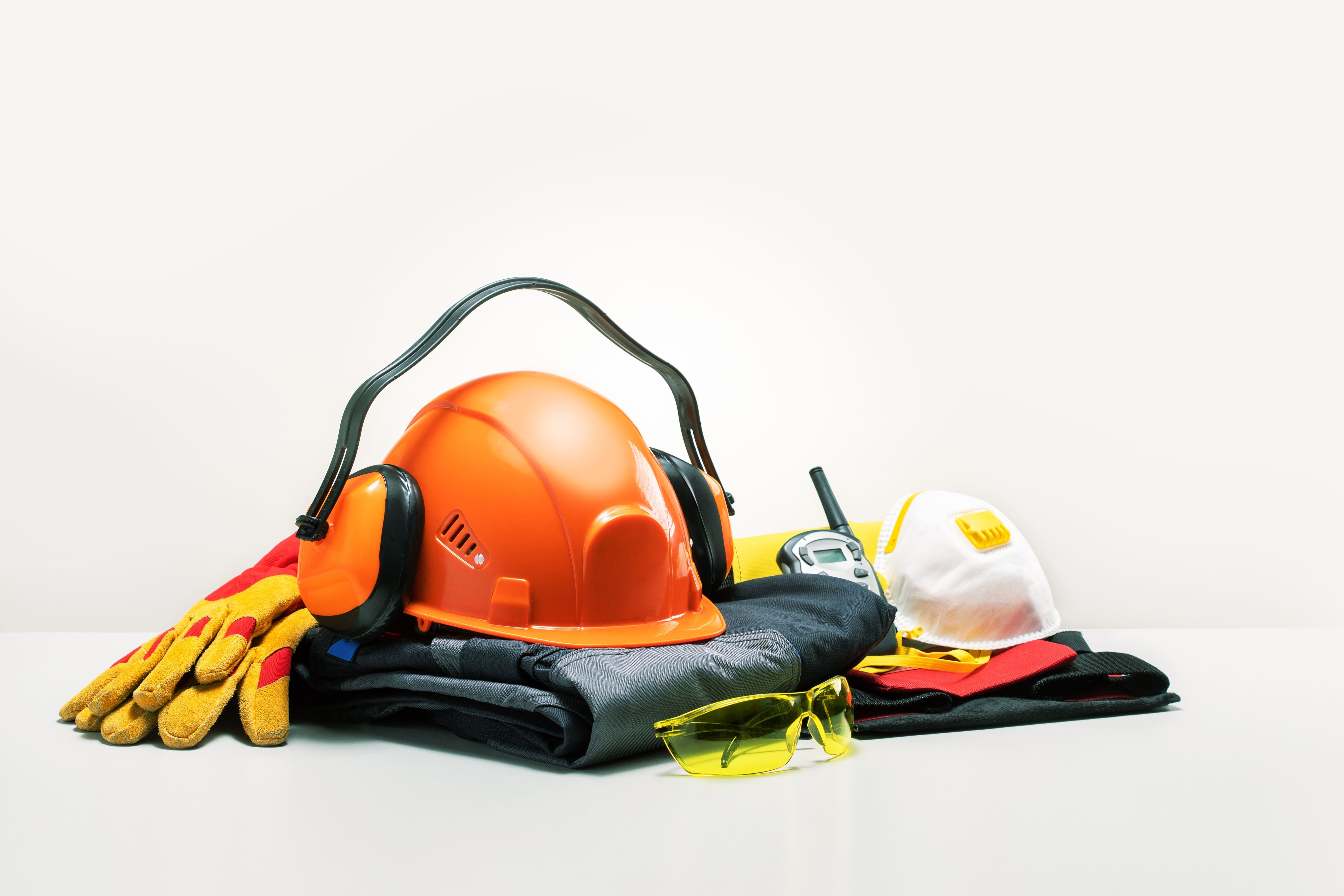
Understanding OSHA's New Construction PPE Requirements
18 February 2025 - Evotix
The Occupational Safety and Health Administration (OSHA) has recently revised standard 29 CFR 1926.95(c) for construction personal protective equipment (PPE). The final rule, which took effect on..
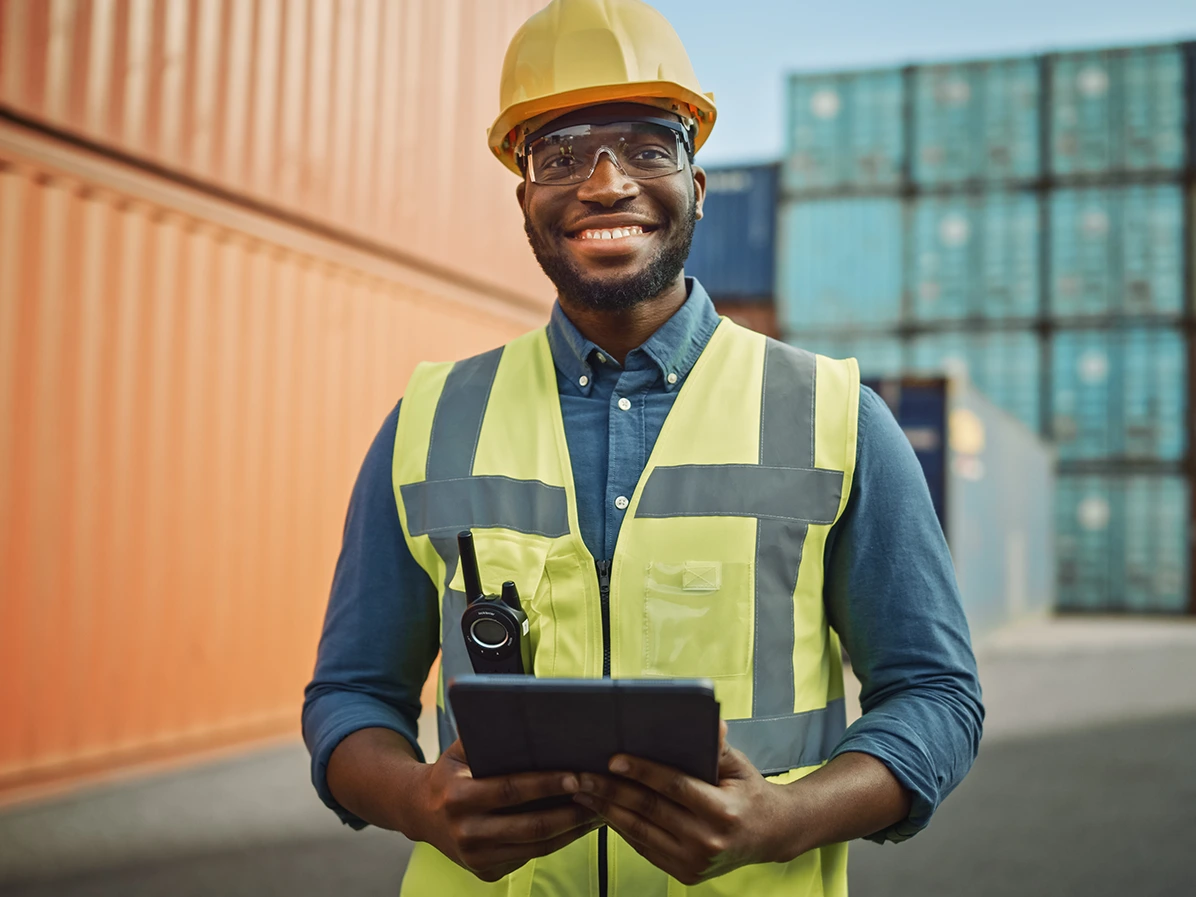
What Is an EHS Audit? Understanding the Basics
13 March 2025 - Evotix
While it’s essential to establish health and safety practices at your workplace, the work doesn’t stop there. Health and safety professionals need to constantly review safety measures to ensure..