Contents
Lost Time Incident Rate – A Complete Guide to LTIR
8 February 2024 - Evotix
In the world of health and safety, it can sometimes feel like everything has its associated metric. But while most metrics are important for reporting purposes, some can also offer valuable insights into your operations. Using these metrics in the right way can give you a far deeper understanding of business performance.
The Lost Time Incident Rate (LTIR) measures productive time lost after every incident and calculates it across the company. Your LTIR helps you understand the business impact of every single incident. This helps you highlight issues and identify steps to mitigate risk going forward.
If business productivity matters to your business, (and it probably does) then the LTIR should not be ignored!
What is Lost Time Incident Rate (LTIR)?
A Lost Time Incident (LTI) is a work-related accident that leads to an employee’s absence from work due to injury or illness. The Lost Time Incident Rate (LTIR) measures this across the whole business, providing a comprehensive view of how LTIs impact a business’s productivity by looking at the total time lost to incidents.
The severity of each incident can vary - from temporary strains that cause minor disruption to more serious, or even long-term disability. The LTIR is a measure of the business impact of this disruption.
Developed by the Occupational Safety and Health Administration (OSHA), the LTIR is a legally required metric in many industries. High rates can lead to a company being investigated. But rather than viewing it as another measurement with the potential to trip them up, companies should be recognizing the potential of this figure to help drive business improvement.
Unlike the Total Recordable Incident Rate (TRIR) which calculates the number of recordable incidents per 100 full-time workers, the LTIR takes the calculation one step further, looking at the time lost to those incidents. As it only considers incidents that result in more than one day away from work, the figure helps you understand the business impact of those incidents and ultimately the effect on a business’s productivity.
How to calculate your Lost Time Incident Rate (LTIR)
To calculate your LTIR you need:
-
Number of Lost Time Incidents (LTIs) in the reporting period
-
Total number of hours worked during reporting period by all employees
When you have those figures, you can complete this calculation:
Number of LTIs x 200,000 / total number of hours worked by all employees
The 200,000 figure represents 100 employees working 40 hours a week in a 50-week year. The idea behind this is to allow fair comparison between companies of different sizes.
In making the calculation, it is important to exclude:
-
The day of the injury or onset of illness
-
Days that the employee would not automatically have worked (vacations)
If these simple rules are followed, the LTIR can provide a very accurate snapshot of your safety status.
Why tracking LTIR is important/why does it matter?
The individual figure may be important for reporting purposes and required by OSHA. But by tracking your LTIR over time, you can get a far deeper understanding of safety trends within your business. Tracking your LTIR matters because it gives a clear sense of the effectiveness or otherwise of the company’s safety program. You can see whether the impact of incidents is increasing or decreasing and therefore whether the measures you are taking are working.
Obviously, the aim for every business is to get the lowest possible LTIR. A lower score means fewer incidents and less impact on the business.
High numbers inevitably raise red flags right across the business:
-
Insurance premiums are higher if a business is deemed less safe
-
Reputational damage can be widespread, leading to deserting investors and customers (both existing and prospective)
-
Employee morale sinks and workers might look to move to somewhere they feel safer
It is worth noting that LTIR figures are always lagging indicators of safety. They look backwards, assessing incidents that have already occurred. This is helpful since they highlight the impact of past events but provide no indication of a company’s safety performance going forward.
The burden is on the management team to flip the metric into a positive and use it as a learning tool to drive improvement:
-
Highlighting gaps in safety procedures or the need for new initiatives
-
Flagging problems at an early stage before the need for official OSHA intervention
-
Identifying opportunities to support employees in their journey back to health and work
What is a good LTIR?
While the aim is always to get the lowest LTIR rate possible, there will be huge variation between industries. Working in the office of a marketing company will be inherently less risky than working on a construction site and the rate of incidents will reflect that.
The important thing is to assess company performance against industry averages. The US Bureau for Labor Statistics records the industry benchmarks, allowing companies to see how their rate compares to industry norms.
Alarm bells should be ringing if your rate is increasing. That is when it is time to investigate if anything is going wrong with your safety measures and correct them.
Steps to maintaining a low LTIR
The old adage, prevention is better than cure, holds true in this case. A robust safety program will prevent incidents in the first place. However, keeping the rate as low as possible requires a continuous and concerted approach. By taking the following steps, you can make sure you keep your LTIR as low as possible:
Assess – the greater awareness the company has of the risks within the business, the more robust the measures put in place to mitigate them. And this assessment should not be carried out once and then forgotten; it needs to be regularly carried out to make sure that potential new risks are included.
Plan – a comprehensive plan that takes account of all potential hazards should also attribute distinct responsibilities and outline timelines so that everyone is clear what is required of them and when.
Train – education of staff and increasing awareness of procedures is crucial to the success of any safety program. Additional training courses or refresher sessions may be necessary to keep all staff members up to speed and ultimately to prevent incidents.
Learn – if an incident does occur, then a full investigation following it is important to make sure the right lessons are learned and there is not a repeat in the future.
As a metric, the LTIR does so much more than just record time lost to incidents. It shows the direct correlation between incident and business productivity. Tracked over time, it can be valuable in helping you spot developing trends, explore the overall safety performance of your company and measure the effectiveness of your safety program. By using this figure to better understand business performance, you can clearly demonstrate that safety and productivity go hand in hand.
Want to dive deeper into efficient incident management? Check out our blog: The Ultimate Guide to the Importance of Incident Reporting
RELATED BLOGS
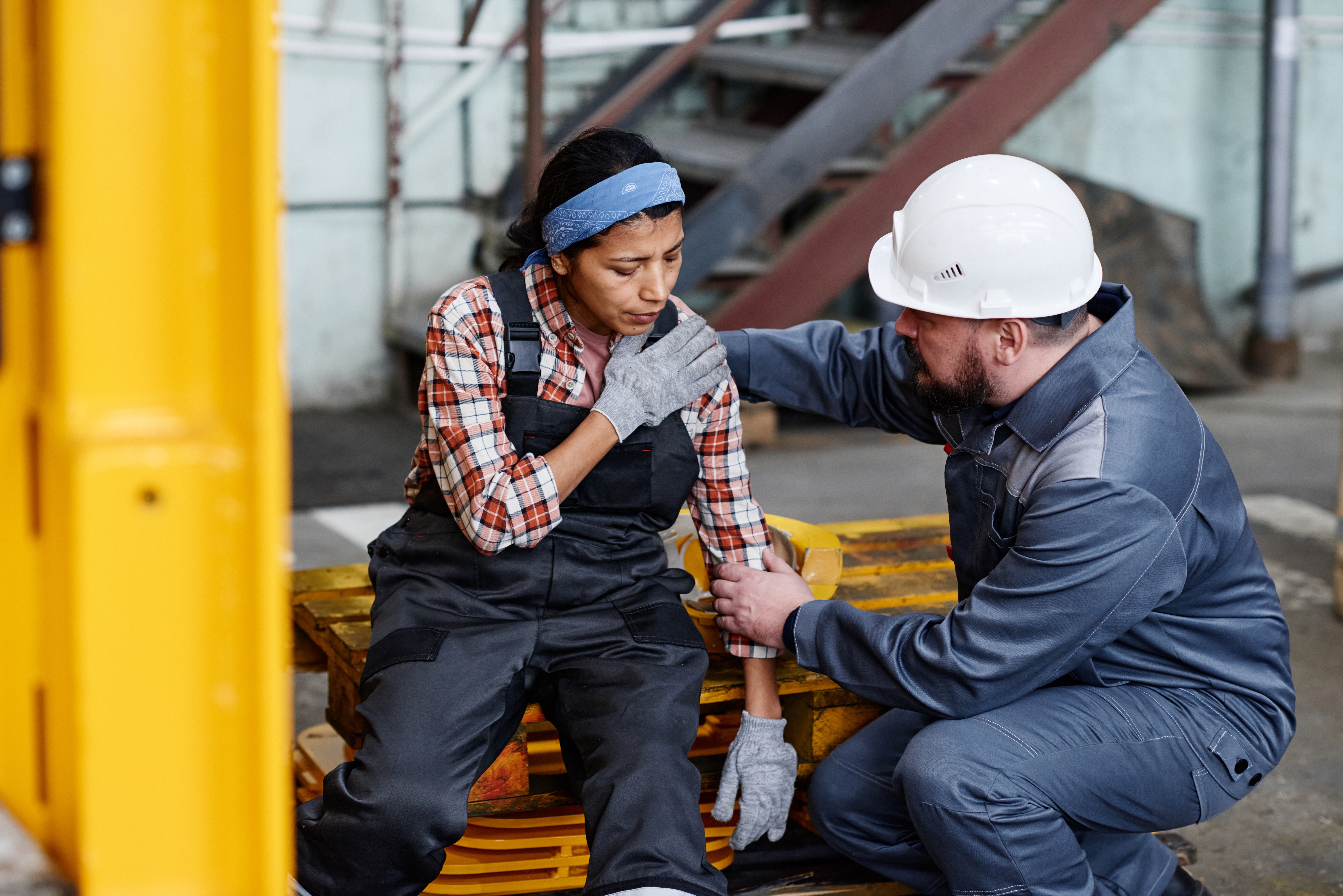
How Incident Reporting Software Can Help Prevent Future Incidents
13 June 2024 - Evotix
Every incident in the workplace has far-reaching implications for the business. Impacting not only the individual worker affected, but the morale of the whole team and their confidence in the..
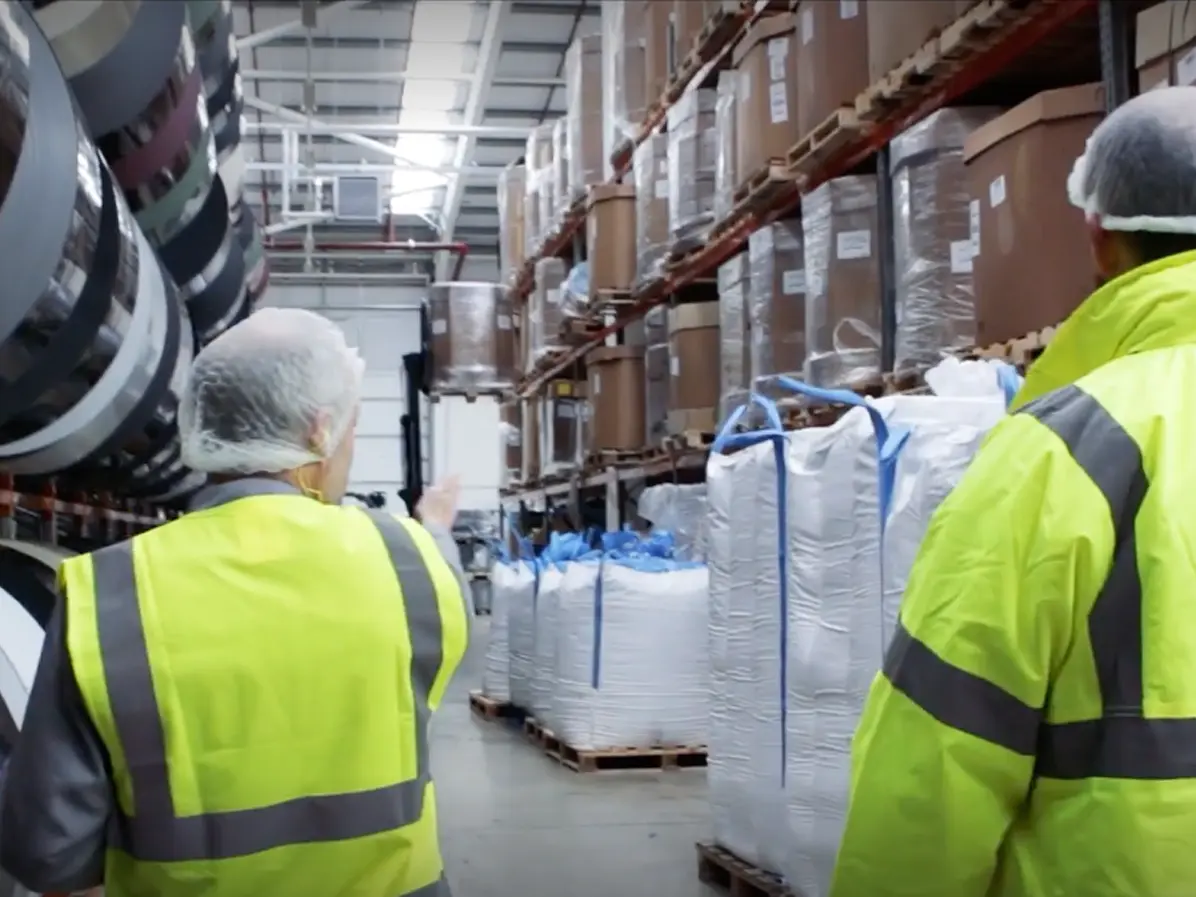
The Ultimate Guide to the Importance of Incident Reporting
6 November 2024 - Evotix
Incident reporting is essential for maintaining a safe and compliant workplace. Thorough documentation of every workplace incident, no matter how minor, helps prevent future, potentially more serious..
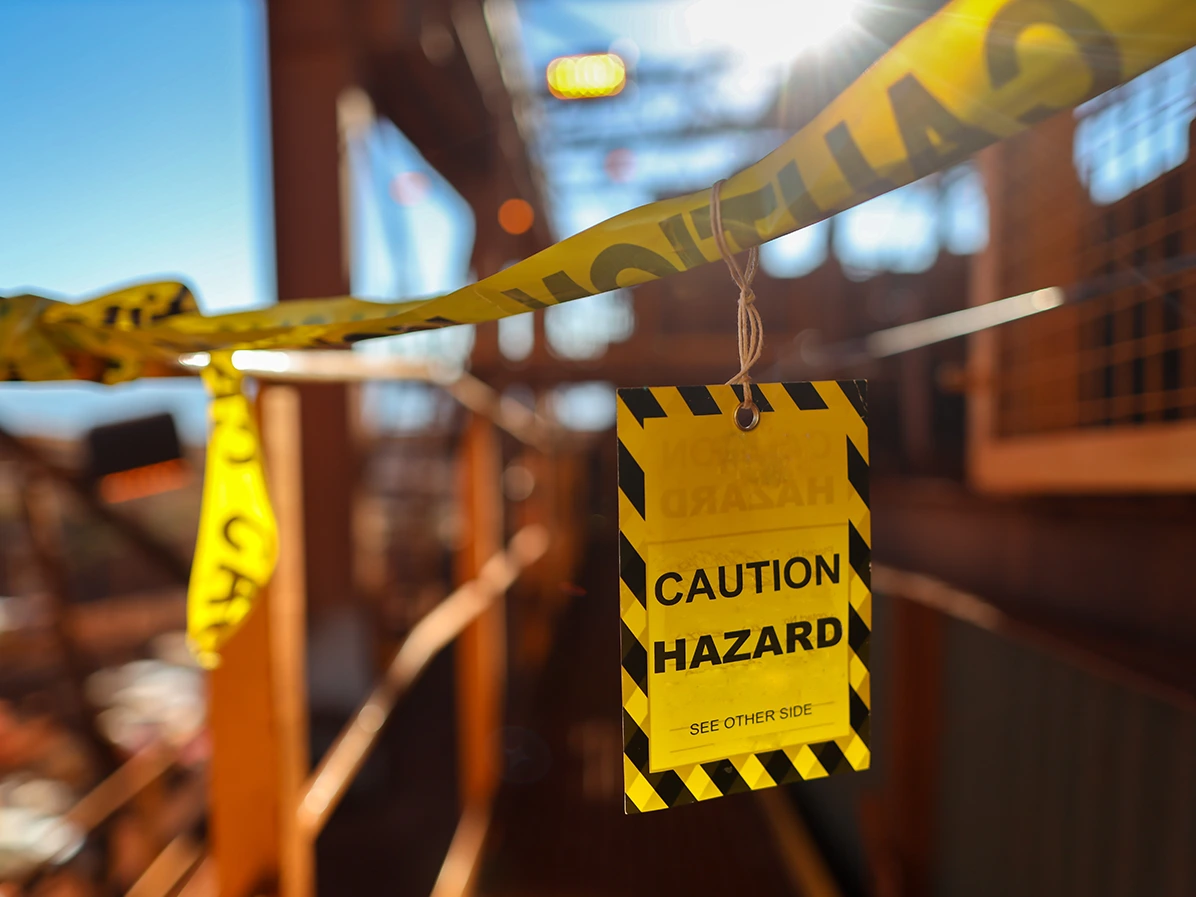
What Is Safety Incident Management and Why Does It Matter?
14 February 2023 - Evotix
Today, workplace accidents still occur all too frequently. In North America alone, 2022 saw 2.6 million reported workplace accidents and illnesses. There are many reasons for workplace incidents to..