Contents
The Complete Health and Safety Audit Checklist
15 November 2024 - Evotix
Workplace health and safety is essential for every organization. Prioritizing employee well-being not only boosts productivity and morale but also improves overall quality of life. While hazards are common, organizations that focus on mitigating these risks are more likely to prevent incidents, creating safer and more productive workplaces. Protecting both the physical and mental health of employees leads to a stronger, more efficient organization.
To help ensure the accuracy of the controls in place, you need to make sure your organization is maximally prepared. Safety procedures should be properly implemented according to official guidelines.
A health and safety audit is a great way to ensure no steps are missed and that a process is created to guarantee health and safety remains more than just a priority for the organization.
What is a health and safety audit?
A health and safety audit is a high-level assessment of organizational health and safety. The audit investigates a company’s health and safety policies, processes, procedures and systems to identify what gaps are present and the steps needed to accurately mitigate the risks and hazards in the workplace. Additionally, it is an excellent tool that shows the aspects of continuous improvement to an organization’s health and safety.
Usually, an audit is heavily reliant on the industry of the organization. It should be detailed and comprehensive, containing all elements of the workplace that need regular maintenance and check-ups. The audit checklist should include potential risks and indicate the likelihood and severity of the risk and hazard impact.
A health and safety audit should be used every time you prepare or conduct an audit. Likewise, the audit checklist is a helpful tool during inspections. The frequency of an audit will typically depend on the risk level of your organization.
A health and safety audit checklist may inspect elements such as fire, electricity and building safety risks.
Who needs to use a health and safety audit?
Any business with a workplace is required to use a health and safety audit checklist. This is an important step towards ensuring compliance with relevant regulations from organizations such as OSHA, HSE and Safe Work Australia.
By following a checklist, a business can ensure they are meeting each specific requirement, without missing anything important. Businesses that want to improve their safety standards will also benefit from using an audit checklist, to ensure best possible results.
Health and safety audit checklists are used by the health and safety department and any other team members in charge of inspections.
What should be included in a health and safety audit checklist?
A health and safety audit checklist should be tailored to industry-specific regulations, ensuring each step is relevant to creating the safest possible work environment.
Here are 7 steps for a health and safety audit checklist. Keep in mind, these steps are examples and may not apply to every organization, as each checklist should be customized to fit industry needs:
1. Personal Protective Equipment (PPE)
-
Have employees received the necessary training around the correct use of PPE? This should include use and removal.
-
Is the PPE in the correct condition for the safest result?
OSHA requires the employer to assess whether the workplace necessitates PPE. The employer is then required to select the appropriate protective gear and communicate proper usage to their employees through training.
2. Tools and Machinery
-
Are all the dangerous, complex or heavy machinery in use regularly checked?
-
Is the machinery in good condition?
-
Does it pose a threat to employees?
-
Are all employees adequately trained to operate the machinery to the safest standard?
Tools and machinery are present in many industries and even simple tools can be hazardous if used inappropriately. Regulatory bodies will have specific standards for each tool.
3. Electrical
-
Are the necessary safety equipment and procedures in place around all the electrical elements in the workplace?
-
Is adequate lighting provided across the workplace for employees to work effectively and safely?
Most industries work with electricity, either directly or indirectly. Engineers and electricians specifically may work with overhead lines and cable harnesses, while office workers may have indirect exposure to electricity.
OSHA, HSE and Fire Safety Australia have long recognized electricity as a potentially serious workplace hazard and specific guidelines should be followed to avoid events such as electric shock, electrocution, fires and more. These specific standards and guidelines can be found on your country’s relevant health and safety website.
4. Fire
-
Are the correct procedures in place regarding a clear fire safety evacuation?
-
Are clear evacuation routes and an adequate number of fully working fire extinguishers provided?
-
Are employees aware of fire emergency protocols?
Fire is a possibility in many workplaces. All employers should provide fire emergency training and a fire plan should be in place. For exact guidance on standards in your industry, visit your relevant regulatory body’s website.
5. Heavy Loading/Unloading
-
If your workplace requires regular loading and unloading of heavy goods, are there properly functioning ramps and platforms and properly working loading arms?
-
Are all junction boxes and wiring in good working order?
Heavy loading and unloading will be particularly relevant to the transportation sector. There are many considerations when it comes to measuring the safety of your loading and unloading areas and relevant guidelines should be carefully followed.
6. Chemical/Hazardous Substance Storage
-
Are the correct procedures in place for the usage and storage of chemical/hazardous substances? This should include correct temperatures, safe storage containers, proper labelling of products and the necessary equipment to deal with these substances safely.
-
Are employees dealing with these substances properly trained in line with the stated regulations?
Chemical hazards pose a wide and serious hazard threat. Per OSHA’s and HSE’s guidance, employees working with chemicals should have information readily available on chemical hazards and toxic substances. Employees should also be aware of all possible risks before handling the chemicals.
7. Working from Height
-
Is clear evidence provided that all equipment used by employees when working from height, such as step ladders and elevating devices regularly checked?
-
Are weight restrictions clearly labeled and adhered to?
-
Is the equipment grounded correctly when in use and is all electrical equipment properly maintained?
-
Are employees trained on how to use ladders safely?
Working from height is a hazard usually experienced predominately by construction and electrical companies. All work conducted at height should be well planned in advance and supervised, according to websites such as OSHA and HSE.
Health and safety audit schedule
Along with key criteria, a health and safety checklist should offer guidance on scheduling. Some items may need more frequent monitoring, depending on industry standards and audit timelines. Clear instructions for regular inspections help maintain regulatory compliance and ensure that no area of the workplace is overlooked.
Health and safety audit checklist template
Health and safety audits are an important part of the overall health and safety of your organization. A well-detailed and relevant audit checklist can help ensure your compliance with regulatory measures and prepare your organization to pass audits.
Health and safety audit checklists vary widely across industries and businesses. EHS software can simplify the creation of a customized checklist with all the criteria relevant to your organization. This software streamlines the audit process, offers mobile access and ensures compliance with recognized standards. Key features to look for include monitoring, image attachments, feedback options, automated reports and dashboard data generation.
A well-designed audit checklist enables detailed workplace inspections, helping your organization pass audits, avoid legal fines, and, most importantly, protect employees effectively.
A safety audit checklist ensures that your organization is actively identifying and rectifying potential dangers. Want to lean more? Click below!
RELATED BLOGS
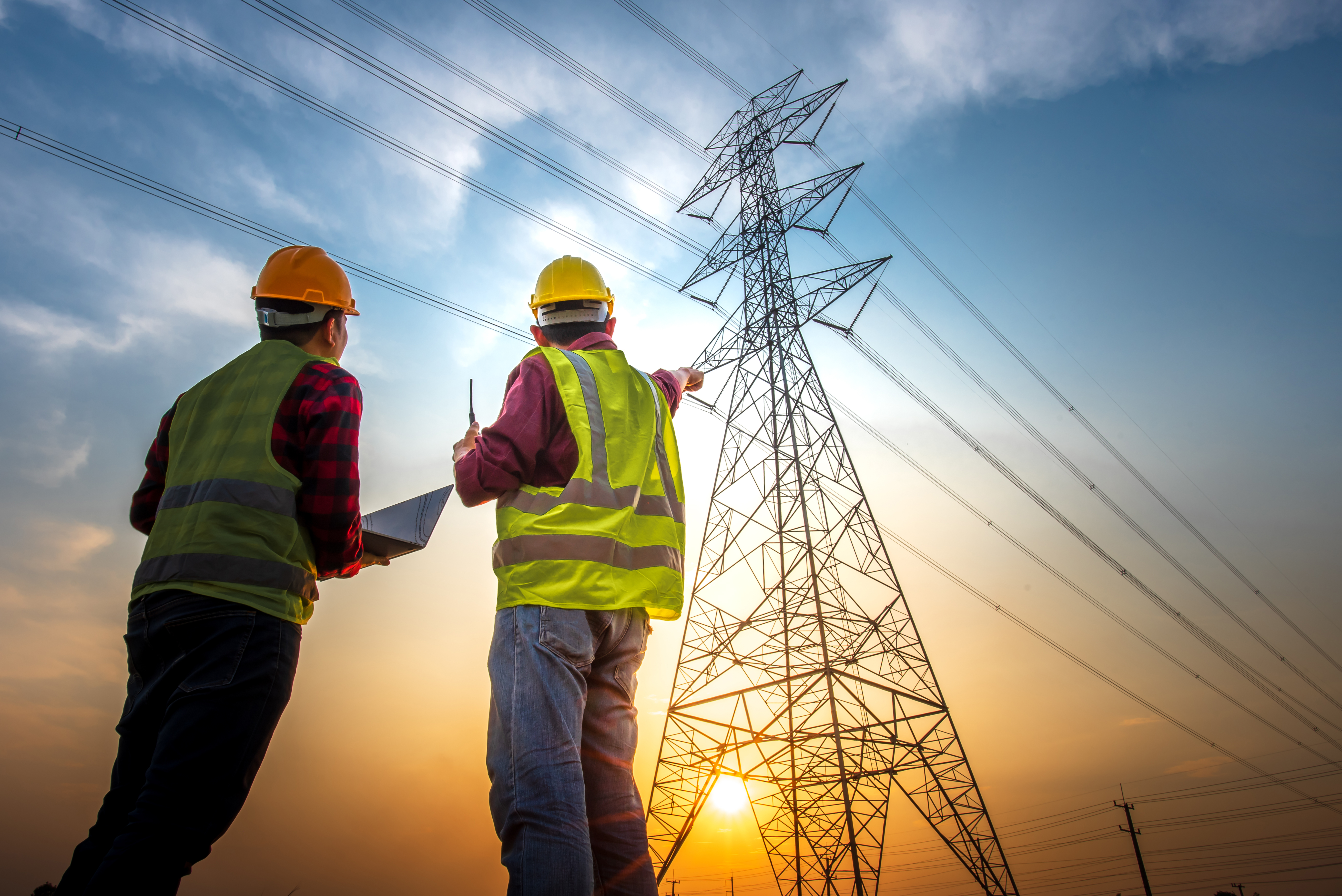
The 5 Key Components of a Safety Audit
14 November 2024 - Evotix
Safety audits are essential for upholding health and safety standards across your organization. Beyond meeting legal requirements, they help proactively identify and address potential hazards that,..
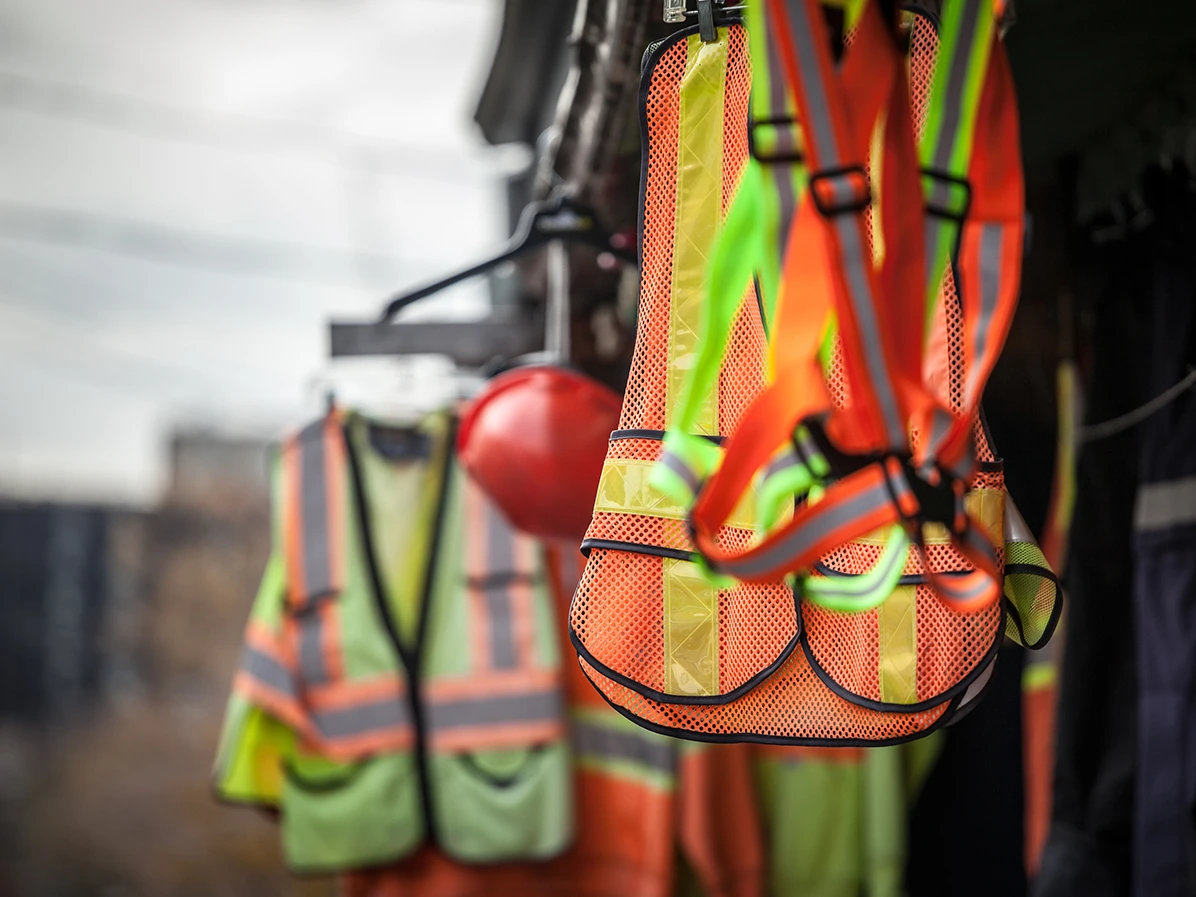
What To Look For When Sourcing PPE
25 April 2023 - Evotix
Personal protective equipment (PPE) is an essential part of ensuring the safety and well-being of employees. Whether you are in construction, healthcare or manufacturing, it is important to devote..
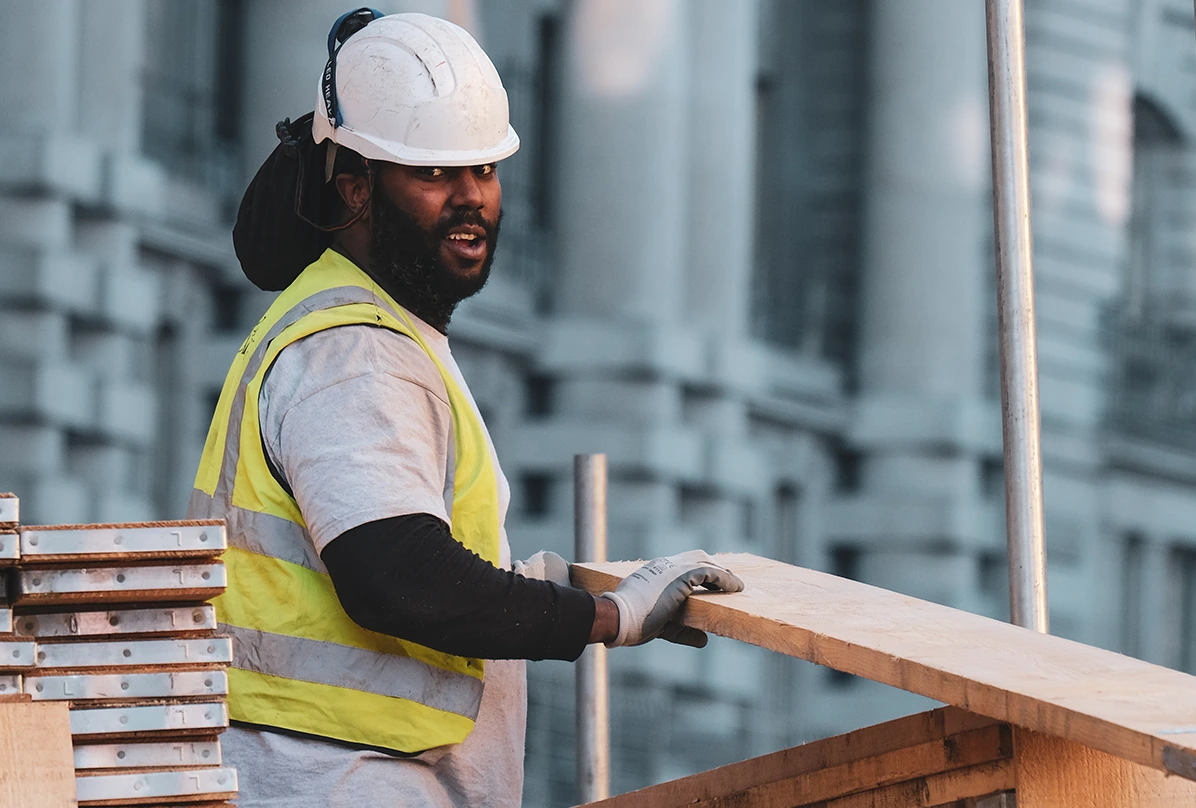
The Importance of Health & Safety in Construction
17 November 2022 - Evotix
Construction is an inherently dangerous profession. From working at heights, to operating heavy machinery and using tools, the tasks undertaken by the typical construction worker are more..