Contents
Top 5 Safety Hazards In the Manufacturing Industry
14 June 2024 - Evotix
According to the National Safety Council, in 2022, the manufacturing sector reported 110 non-fatal injuries per 10,000 workers, making it the sixth highest ranking industry for such injuries. With an estimated 13 million workers at risk, this sector accounts for 8% of the U.S. workforce, according to the National Association of Manufacturers.
Hazards not only threaten employee well-being, but they also undermine an organization's efficiency.
In many manufacturing environments, safety often takes a backseat as companies face constant pressure to perform better, reduce costs and stay competitive. It's crucial to recognize that prioritizing safety can significantly boost a company's productivity. Organizations that invest in safety not only enhance productivity but also reduce time and financial losses. It's time for more leaders to view health and safety as an asset, not a burden.
1. Falls From Height
Working with heights presents one of the most serious safety concerns for the manufacturing industry. Yet, this doesn’t mean that a worker can only be injured when working at skyscraper level. In fact, most height injuries occur at less than 10 feet above the ground, according to Fire & Safety Australia.
Falls frequently occur while workers are over-reaching, attempting to access machinery, balancing on uneven surfaces, working on mezzanines, elevated platforms or working on loading docks. Unguarded holes, water sources and falling objects are also aspects of height that can lead to serious injury. These can easily be overlooked when talking about working safely from heights.
When working from a height, thorough and regular workplace inspections should be carried out, guardrail and fall arrest systems should be put in place and training should be provided.
Employers are responsible for providing their employees with the information and protection necessary to ensure height safety. Due to the 2005 UK Work at Height Regulations law, regulations are in place for employers to control work at height. Employers are legally required to ensure that height work is planned, supervised and carried out competently and properly.
2. Electrical hazards
Workers in the manufacturing industry are frequently exposed to and work with electricity. The main hazards of working with electricity include electric shocks, fires from faulty electrical equipment, overhead powerhead lines, damaged tools, damaged insulations and even explosions. An incident’s severity can be exacerbated when working at height or during wet conditions. Employees may suffer from electric shocks, burns, falls, muscle spasms or heart problems as a result.
More and more companies are now actively pursuing safe electrical practices. Thanks to the NFPA 70E, Standard for Electrical Safety in the Workplace, U.S. employers are required to establish electrical safety programs, work policies and procedures. According to OSHA, employers must conduct appropriate shock hazard and flash hazard analyses. Optimal electrical safety stems from awareness, proper instruction and hazard identification. Electrical equipment must be maintained regularly and everyone working with electrical equipment must have appropriate electrical skills and knowledge.
3. Poor Maintenance
Inadequate maintenance directly correlates to negative health and safety outcomes in manufacturing. Machinery, equipment and workspaces that are not maintained properly may cause serious health problems, incidents or injuries. Even fail-safes can fail, yet regular maintenance can help catch malfunction by shutting down machinery immediately.
Similarly, maintenance of workspaces, such as walkways and mezzanines must be carried out to ensure there are no trip hazards. Maintenance ensures proper air quality, as well as a lack of leaking fluids, steam, gas or hazardous chemicals. Employee training should be maintained to ensure that all workers are up to date with hazard detection and proper machine use.
Regular maintenance helps minimize costly breakdowns and can help prevent unfortunate incidents from occurring. Taking the time to ensure that your workplace is safe and running with no known hazards, helps organizations avoid lengthy and expensive downtimes. According to the leading manufacturing publication, Supply Chain Brain, the cost of each equipment downtime incident averages at about $2 million in expenses in manufacturing. When equipment, workspaces and machinery are maintained, work can go as planned.
4. Hazardous Chemicals
Manufacturing workers may have to work closely with dangerous chemicals such as caustic cleaning solutions, battery acid and flammable substances. Physical and health hazards associated with toxic chemicals include:
-
Irritation
-
Carcinogenicity
-
Flammability
Unexpected releases of hazardous chemicals can cause serious incidents, usually as a result of improper care. OSHA has issued the Hazard Communication Standard (HAZCOM) to ensure fast and accurate information retrieval in regard to chemicals. This is important in the case of an incident where quick action is necessary to ensure safety. All companies which work with hazardous chemicals must cultivate effective hazard communication to promote safety. Such companies must have clear, visible written programs around the site with important information, compliant hazard labels and provide HAZCOM training.
5. Vehicles
According to HSE, work vehicles continue to be a major cause of fatal and serious injuries. Heavy-duty vehicles pose an especially serious risk as they are larger and heavier, have bigger blind spots and require specific knowledge and experience on behalf of the driver.
Incidents involving heavy-duty vehicles may include falling objects from unsafe loading, injuries as a result of overturning and workers being hit while the vehicle is moving.
Compliance should be followed closely; vehicles should be serviced regularly and the right vehicle should be chosen for each specific job. All operators should be trained extensively and all staff should be briefed thoroughly on safety measures relating to vehicles.
To find out more about how to better protect manufacturing employees from injury, visit our Manufacturing page: https://www.evotix.com/industries/manufacturing-ehs-esg-software
RELATED BLOGS
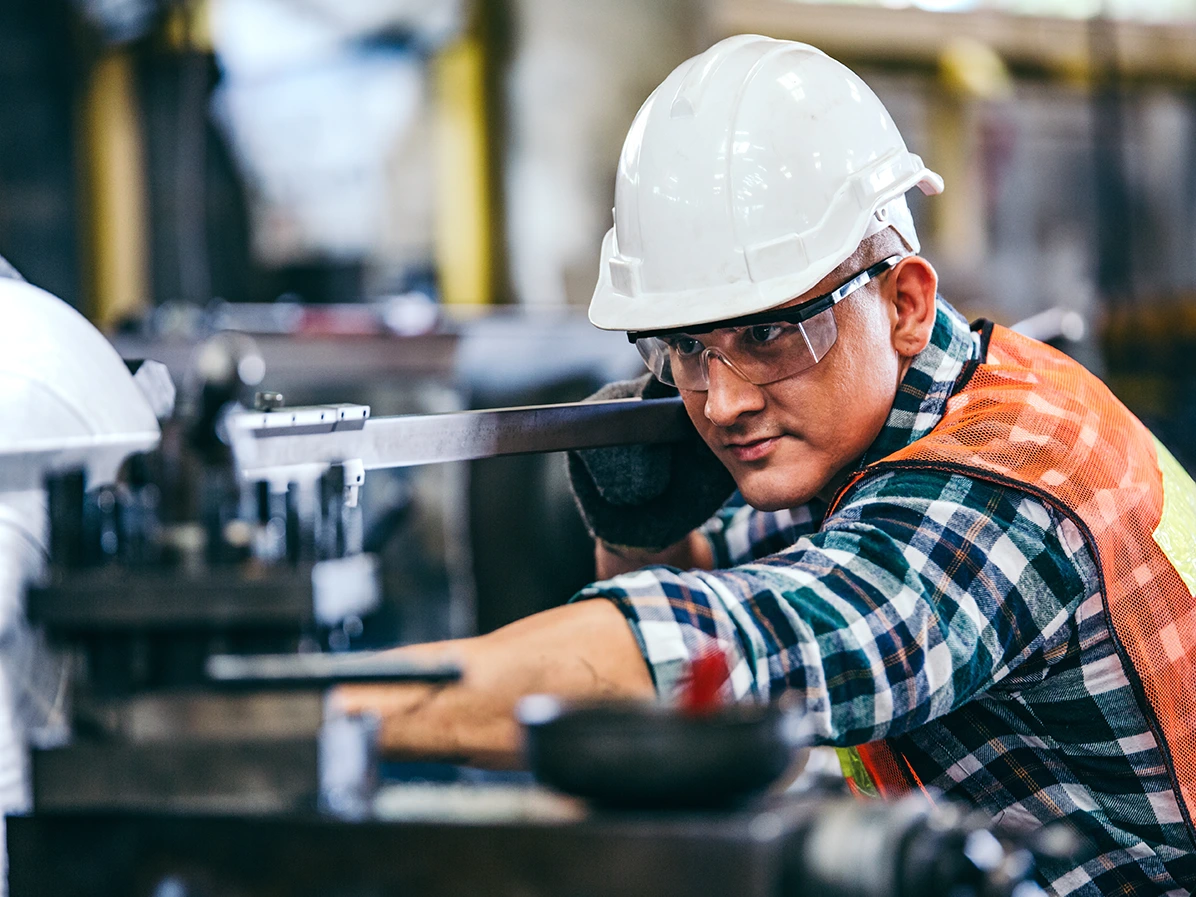
The Importance of Safety in the Manufacturing Industry
27 November 2024 - Evotix
While industries like construction, fishing or hunting often top the list for serious workplace incidents, manufacturing holds a unique and concerning position. Despite employing a smaller percentage..
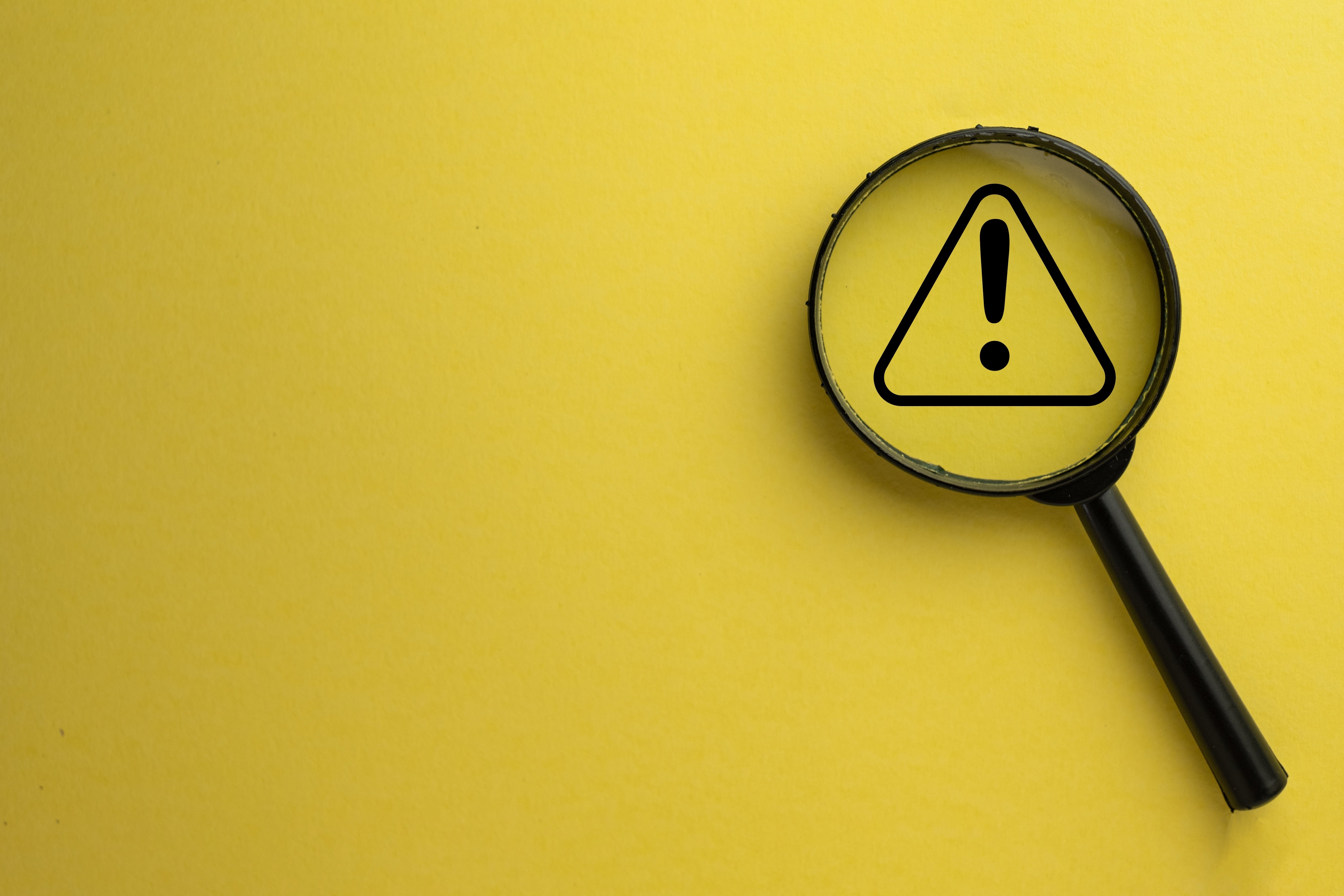
OSHA's 2024 Hazard Communication Standard: What You Need To Know
5 June 2024 - Langdon Dement
Once again, the United States is in the wake of a major change - a change that has been anticipated for three years and is bound to create a stir for organizations. A change that is believed to..
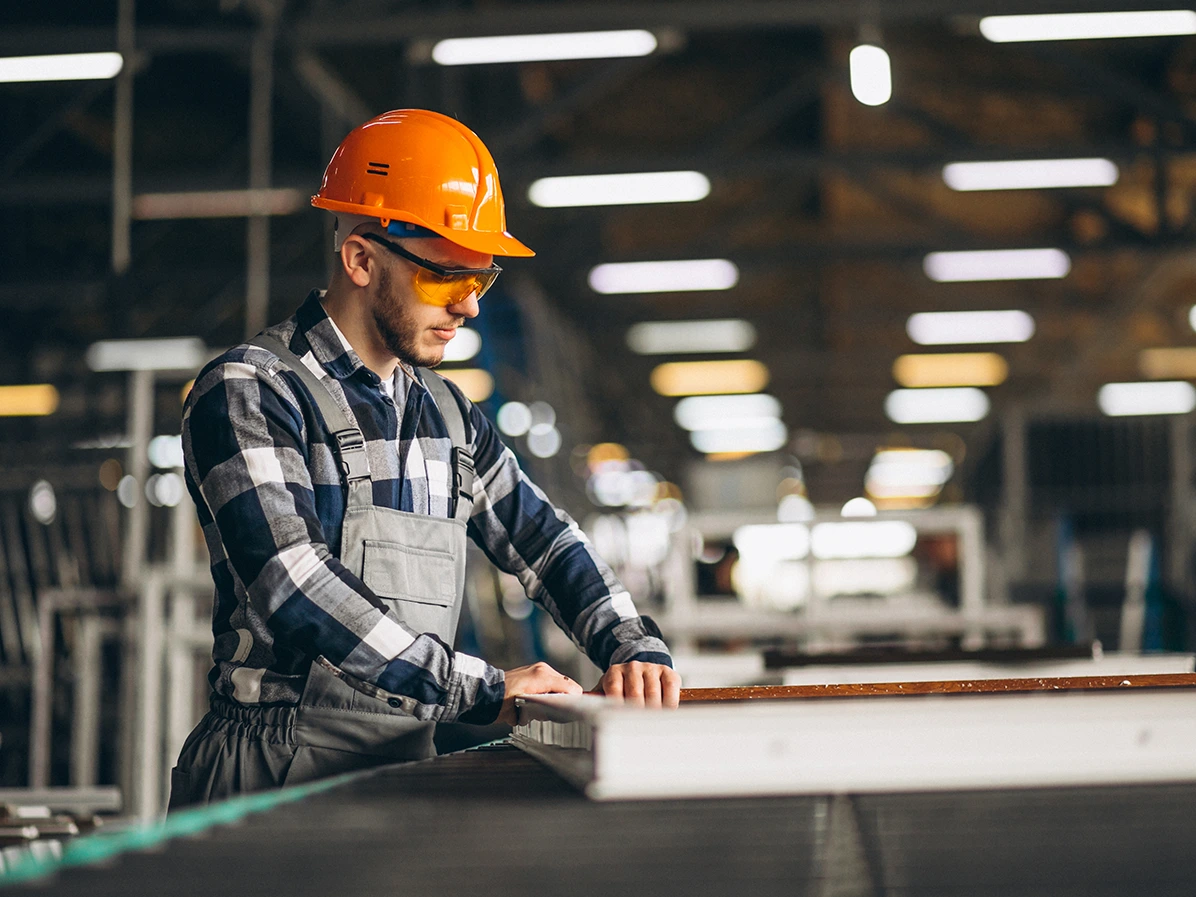
How To Ensure Good Health And Safety Practices In Manufacturing
1 December 2022 - Evotix
The manufacturing industry is an economic powerhouse in the U.S. It’s responsible for producing 20 percent of the nation’s capital investment, 35 percent of productivity growth, 60 percent of..