Contents
Tips for Elevating Contractor Safety To Meet Growing Demand
9 January 2024 - Evotix
Contractor safety management is a highly important framework for companies navigating an era of increasing dependence on contractors. But what exactly is it? It's a fusion of integrated management processes meticulously crafted to reduce risks associated with contractors.
Companies are turning to contractors now more than ever. This especially holds true in the U.S. construction sector, where contractors fill a staggering one in every five jobs. Projections indicate that they'll constitute nearly half of the U.S. workforce in the unfolding 2020s.
Yet, even with strides in safety equipment and training, contractor safety is far from perfect. The construction industry, for instance, grapples with elevated rates of both nonfatal and fatal injuries compared to other sectors. In fact, a harrowing one in every five on-the-job deaths in the U.S. is attributed to construction workers.
By exploring the roadblocks to contractor safety management in industries from construction and manufacturing to mining and agriculture, a pathway to safer practices can be found.
Challenges to contractor safety management
Companies encounter numerous challenges when instituting contractor safety management programs, including:
-
Lack of control: Organizations wrestle with limited control over contractors' safety practices since they aren't typically direct employees, making adherence to organizational policies challenging.
-
Shortage of management tools: The absence of technology for gauging contractor performance hinders companies’ ability to make informed decisions based on performance and security scores.
-
Different safety cultures: Contractors often bring their own safety cultures, leading to potential clashes with the organization's safety policies.
-
Communication barriers: Language or cultural barriers may hinder effective communication, resulting in difficulties in enforcing safety policies.
-
No onboarding process: Absence of a robust onboarding process contributes to communication gaps, undermining the importance of safety procedures for new contractors.
-
Lack of resources: Insufficient resources or personnel disrupts effective monitoring and enforcement of safety policies for contractors.
-
Resistance to change: Some contractors resist adopting new safety practices, posing challenges in implementing updated policies and procedures.
Strategies for ensuring contractor safety
Initiating and sustaining contractor safety begins with ensuring your company recruits contractors with commendable safety records and a commitment to following organizational safety standards. Prequalification processes offer an added layer of assurance, ensuring the employment of safety-conscious contractors.
Implementing comprehensive safety policies and procedures for personal protective equipment (PPE), hazard identification/assessment and emergency response is crucial. Permit management ensures compliance and equips contractors to be on-site safely, a critical step in the safety hierarchy.
Facilitating contractors' understanding of organizational safety procedures through training and communication is imperative.
Regular monitoring and evaluation are essential for adherence to policies and procedures. Safety audits, inspections and incident investigations contribute to continuous verification and insights for refining contractor safety management programs.
The role of technology in contractor safety management
Contractor safety management software is a game-changer, streamlining and automating various contractor safety processes. From prequalification and onboarding to on-site monitoring and proactive management of contracting companies, software plays a pivotal role.
Interactive, real-time dashboards empower companies to visualize contractor league tables, offering metrics on incidents, injury rates, unsafe behaviors and drug and alcohol test results. This instantaneous ranking helps identify contracting companies with stellar safety records.
Centralized data registers simplify recordkeeping, providing easy access to information, renewals, prequalification and specialized contractor statuses for specific tasks. This efficiency ensures the seamless selection of the right contractor for any job.
For the safety of all workers on-site, consider automated and mobile control of work, integrating permit to work, job risk assessment and isolation management. Mobile-ready lockout/tagout (LOTO) processes further streamline equipment and machinery safety procedures.
Many contractor safety management software options allow integration with other EHS modules for a comprehensive view of contractor safety, covering industrial hygiene, occupational health, waste management and more.
Enhancing contractor safety
Companies employing contractors can elevate contractor safety management by embracing these best practices and adopting technology solutions that align with their operational needs. Automation of contractor safety management processes promises improved operational performance, cost reduction and the prevention of potential safety disasters. This approach equips companies to make informed decisions on staffing and health and safety, fostering greater flexibility and alignment with business objectives.
Want to delve deeper into key strategies for effective contractor safety management? Check out our eBook: Contractor Safety Management
RELATED BLOGS
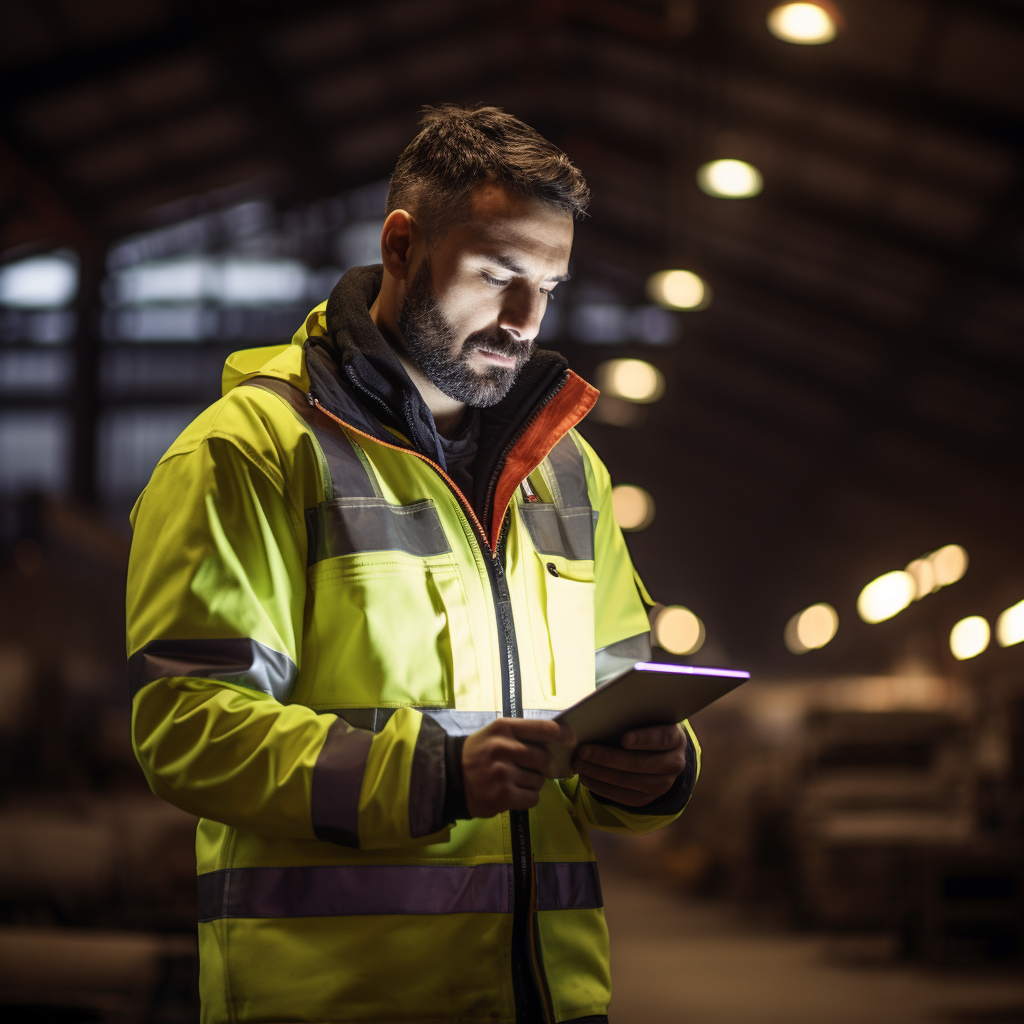
Mitigating Risks: The Advantages of Digital Permit to Work Solutions
3 January 2024 - Evotix
A permit to work (PTW) system is used in industries such as chemical, construction, energy, manufacturing and mining that deal with high-risk operational activities. In these environments,..
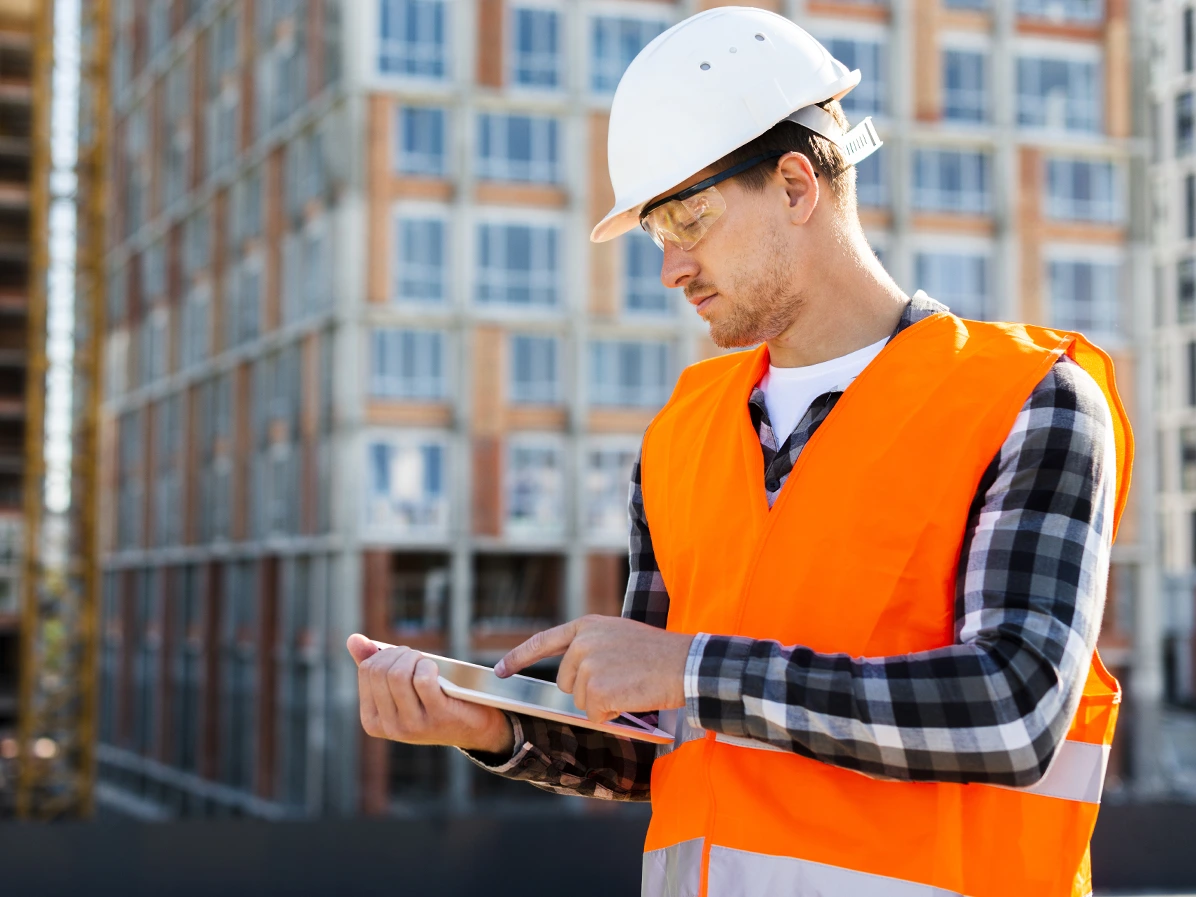
What Is Contractor Safety Management?
21 November 2024 - Evotix
Hiring skilled contractors to address workforce gaps is becoming increasingly common. However, as temporary team members, contractors often bring varying levels of skills, qualifications and..
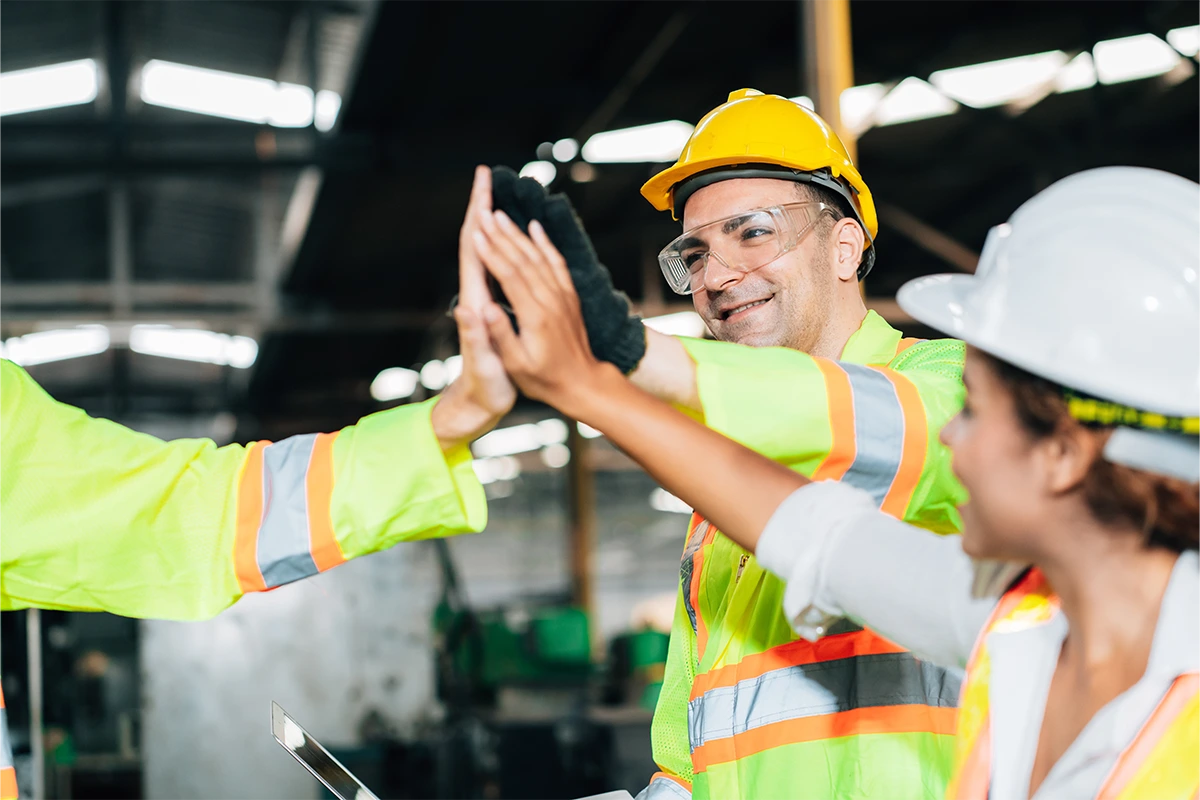
Health and Safety and HR: Working Together to Create Better Workplaces
8 September 2022 - Evotix
HR plays a major role in health and safety. Traditionally, the department responsible for a business’s success and sustainability mainly oversaw the functions of recruitment and payroll. But today,..