Contents
The $1 Billion Cost of Poor EHS Management: Examining the 2024 Liberty Mutual Workplace Safety Index
11 February 2025 - Evotix
A workplace injury can change everything in an instant. For an individual, it may mean physical pain, time away from work, medical bills or long-term consequences. But the effects don’t stop there. For businesses, workplace incidents come with a significant financial burden, including lost productivity, regulatory fines and the challenge of replacing or accommodating injured employees.
Every year, U.S. businesses lose billions of dollars as a result of workplace accidents. In fact, most of these costs (nearly 82.5%) can be attributed to 10 common types of accidents. The Liberty Mutual Workplace Safety Index examines costs from these incident types and provides insights into year-over-year changes. To shed light on where your organization should focus health and safety initiatives, we’ll break down the key findings from this report and demonstrate how your business can reduce costs associated with workplace accidents.
Examining the 2024 Workplace Safety Index
The top 10 most common causes of workplace injuries listed by the 2024 Liberty Mutual Workplace Safety Index cost U.S. businesses over $1 billion per week, totaling over $48 billion for the year. The most common workplace accidents and their associated costs are as follows:
1. Overexertion involving outside sources: $12.49 billion
2. Falls on same level: $9.99 billion
3. Falls to lower level: $5.68 billion
4. Struck by object or equipment: $5.55 billion
5. Other exertions or bodily reactions: $3.68 billion
6. Roadway incidents involving motorized land vehicles: $2.76 billion
7. Slip or trip without fall: $2.34 billion
8. Caught in or compressed by equipment or objects: $2.05 billion
9. Struck against object or equipment: $1.84 billion
10. Repetitive motions involving microtasks: $1.54 billion
Overexertion involving outside sources and falls on the same level have consistently topped the list at #1 and #2 respectively since 2019. New to this list from the 2023 index, however, are #9 and #10, with struck against object or equipment and repetitive motions involving microtasks. These additions replaced harmful substance exposure, which previously held the #6 spot, and pedestrian vehicular incidents, which was ranked #10. This shift reflects a return to pre-pandemic injury trends, as COVID-19-related lost-time claims have been reduced by more than half, dropping from 11% to 4%.
Most Affected Industries
Most of these workplace accidents occurred in just a handful of industries. The total direct costs from serious, nonfatal workplace injuries, along with the top five injury causes for each industry, are listed below.
1. Construction: $10.7 billion
Top five causes: falls to lower levels, overexertion involving outside sources, falls on same level, struck by object or equipment and other exertions or bodily reactions.
2. Professional and Business Services: $8.17 billion
Top five causes: falls on same level, overexertion involving outside sources, falls to lower level, roadway incidents involving motorized land vehicles and struck by object or equipment.
3. Manufacturing: $7.53 billion
Top five causes: overexertion involving outside sources, falls on same level, struck by object or equipment, caught in or compressed in by equipment or objects and falls to lower level.
4. Health Care and Social Services: $6.2 billion
Top five causes: falls on same level, overexertion involving outside sources, slip or trip without fall, roadway incident involving motorized land vehicle and other exertions or bodily reactions.
5. Retail: $5.21 billion
Top five causes: overexertion involving outside sources, falls on same level, struck by equipment or object, falls to lower level and other exertions or bodily reactions.
6. Transportation and Warehouse: $4.71 billion
Top five causes: overexertion involving outside sources, falls on same level, falls to lower level, roadway incidents involving motorized land vehicle and other exertions or bodily reactions.
7. Wholesale Trade: $4.17 billion
Top five causes: overexertion involving outside sources, falls on same level, falls on lower level, struck by object or equipment and roadway incident involving motorized land vehicle.
8. Leisure and Hospitality: $3.41 billion
Top five causes: falls on same level, overexertion involving outside sources, struck by object or equipment, other exertions or bodily reactions and slip or trip without fall.
Key Takeaways From the Workplace Safety Index
With billions of dollars lost each year, businesses must ask themselves if they have done enough to prevent these accidents from happening. To evaluate your current safety strategy, consider these key questions:
-
Have we identified the most common causes of workplace injuries in our industry?
-
Are we investing in training, equipment and processes that directly address these risks?
-
Do our employees feel empowered to report hazards and near misses?
-
Are we regularly reviewing incident data and updating safety measures accordingly?
-
Is leadership actively engaged in fostering safe operations?
Understanding the risks is just the first step. To truly protect workers and reduce costs, businesses must take proactive measures to align their safety investments with the most pressing hazards in their industry.
Using Best Practices To Reduce the Cost of Poor Health and Safety
Investing in injury and illness prevention is the best way to reduce direct and indirect costs associated with workplace accidents, including workers’ compensation, medical expenses and compliance penalties. But how should businesses approach investing in EHS software? Use the following three steps as a guide:
1. Take a Proactive, Rather Than a Reactive Approach
A proactive approach to safety helps organizations prevent incidents before they occur. Unlike a reactive approach that only addresses issues after they happen, proactive safety management focuses on identifying hazards, analyzing trends and implementing preventive measures.
2. Commit to Purpose-Built, Automated Digital Solutions
Despite the obvious advantages of digital health and safety software, many organizations still rely on outdated record-keeping and data management. EHS software not only provides a streamlined, future-proof way to manage data, but it also provides intelligent solutions that can automate tedious routine tasks and give valuable insights into your data.
3. Invest a Little, Save a Lot
For those looking to reduce their bottom line, investing time or resources into health and safety may feel counter intuitive. However, by investing in safety, you can save in the long run. Research has shown that for every $1 invested in safety, companies can save between $2-$6 in direct and indirect costs of workplace accidents.
To learn more about how our powerful safety solutions can benefit your organization, visit our solutions page below!
RELATED BLOGS
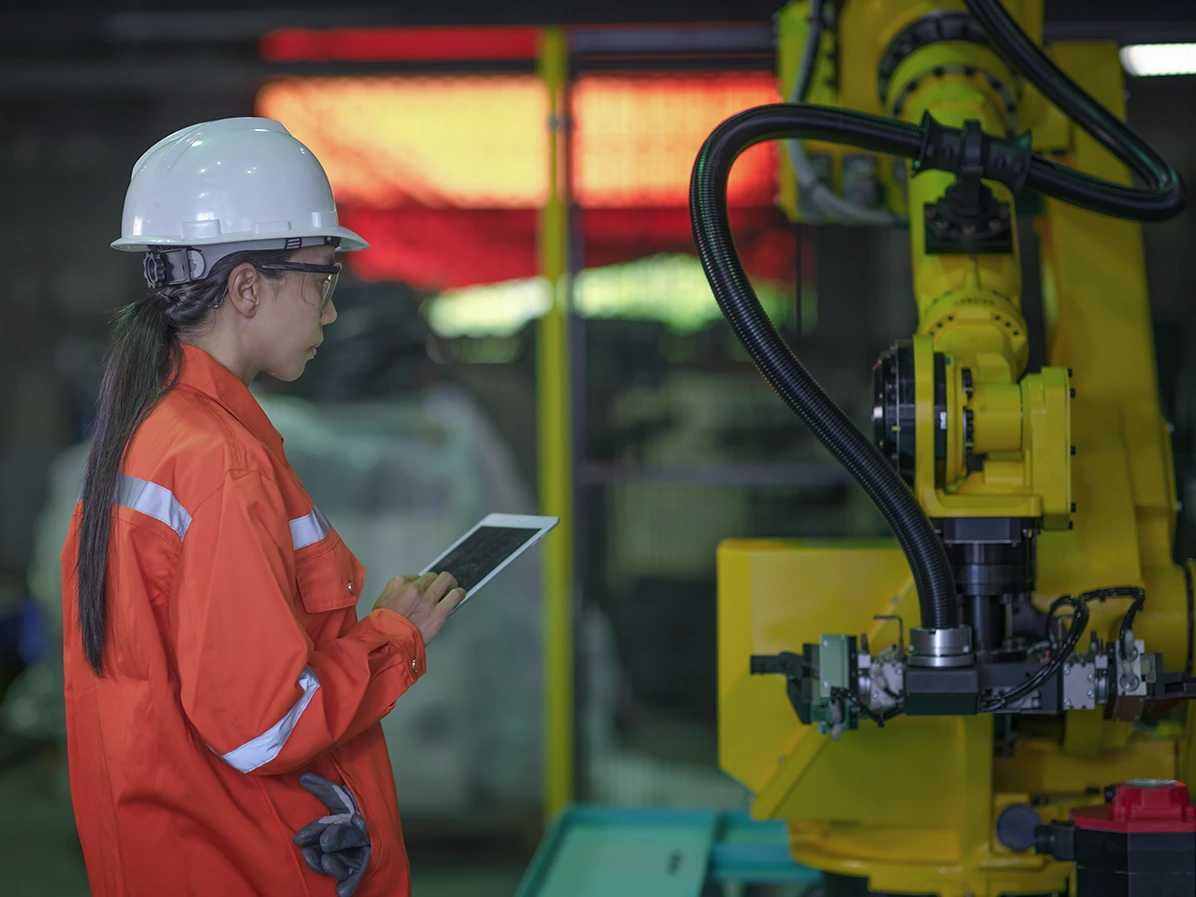
What is Risk Management Software?
1 November 2022 - Evotix
‘Risk management’ sounds deceptively simple—identify what can go wrong, figure out how to ensure it doesn’t, supress the risk. In reality, there are many types of risk that can affect an organization..
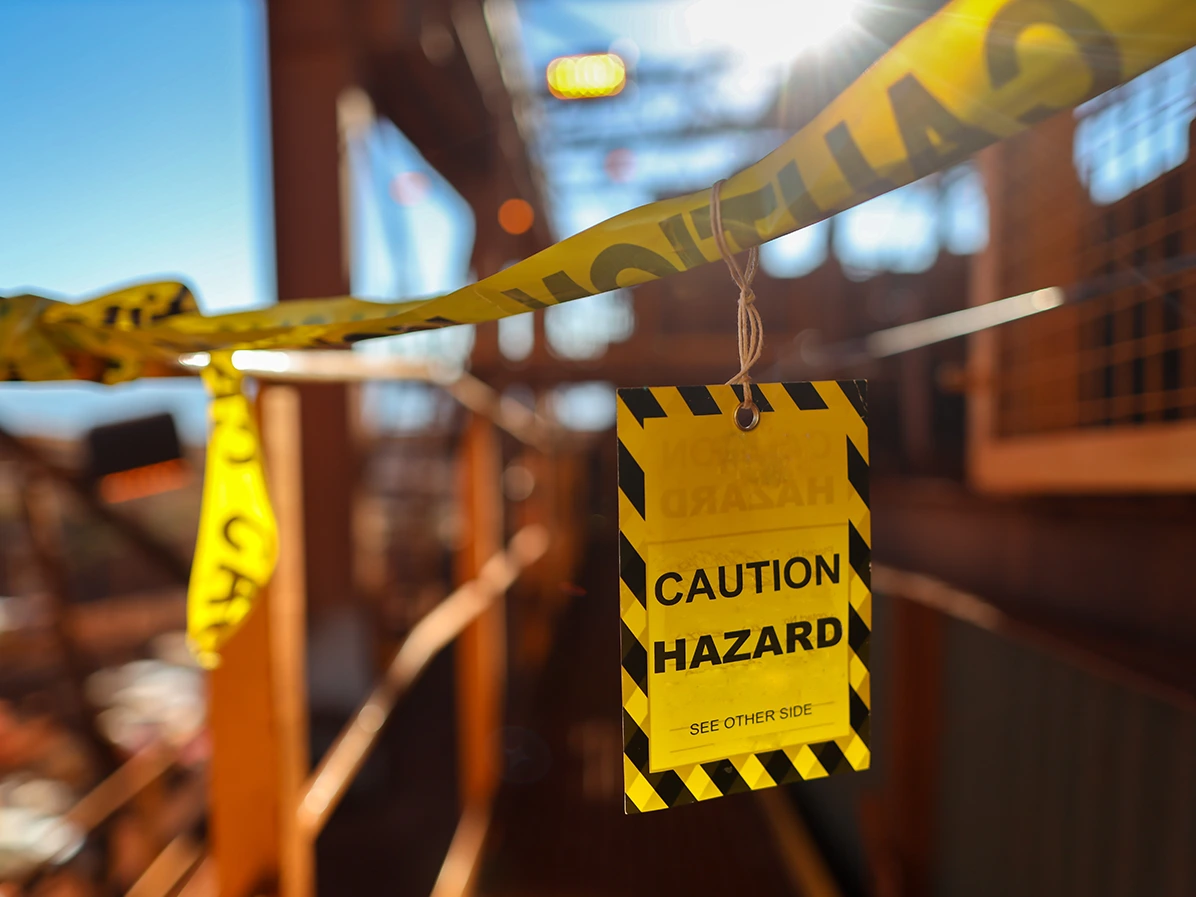
What Is Safety Incident Management and Why Does It Matter?
14 February 2023 - Evotix
Today, workplace accidents still occur all too frequently. In North America alone, 2022 saw 2.6 million reported workplace accidents and illnesses. There are many reasons for workplace incidents to..
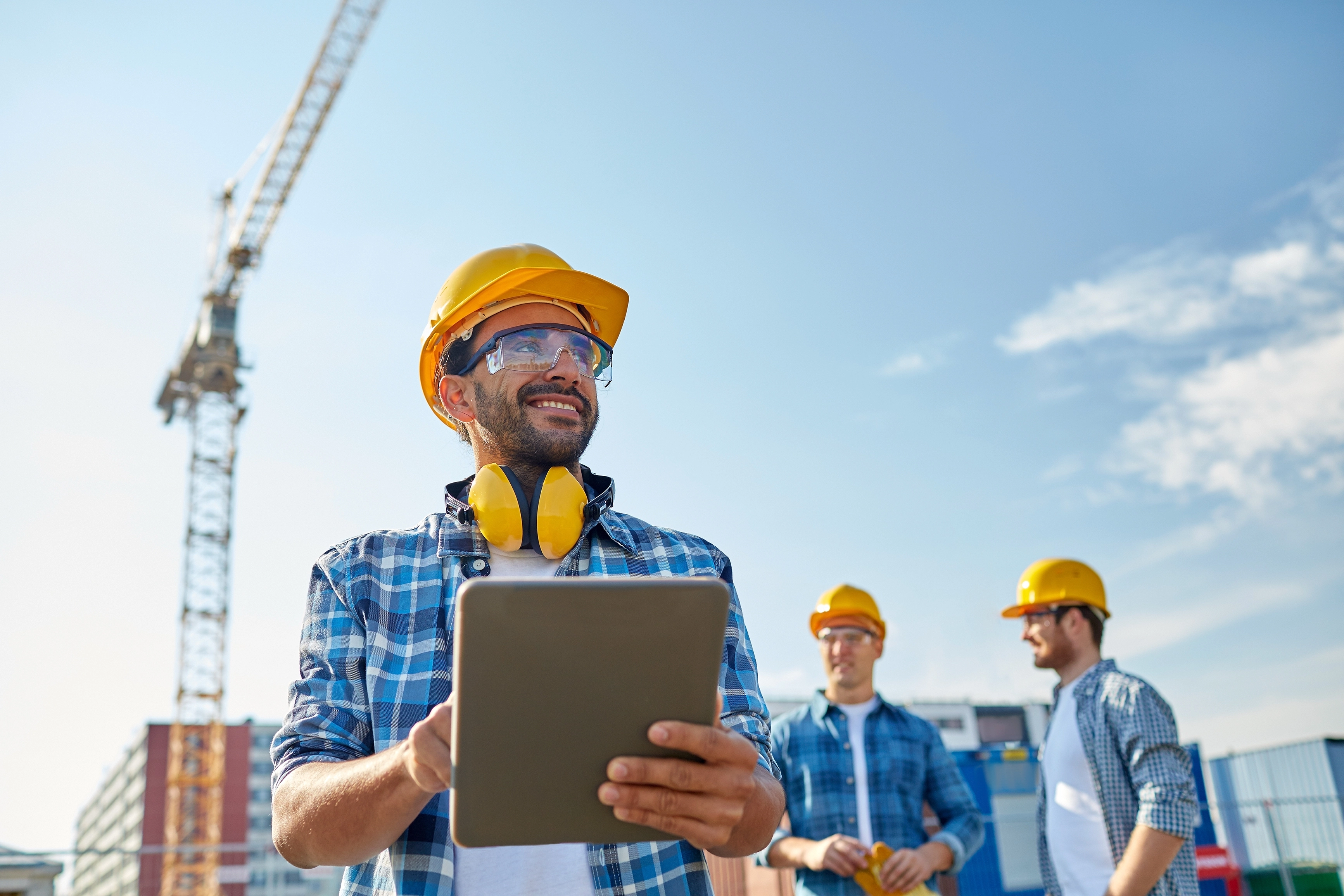
A Strategic Approach to EHS&S Technology Implementation
6 February 2024 - Evotix
Implementing environment, health, safety and sustainability (EHS&S) technology is a crucial step for businesses aiming to create a more proactive approach toward enhancing environmental performance,..